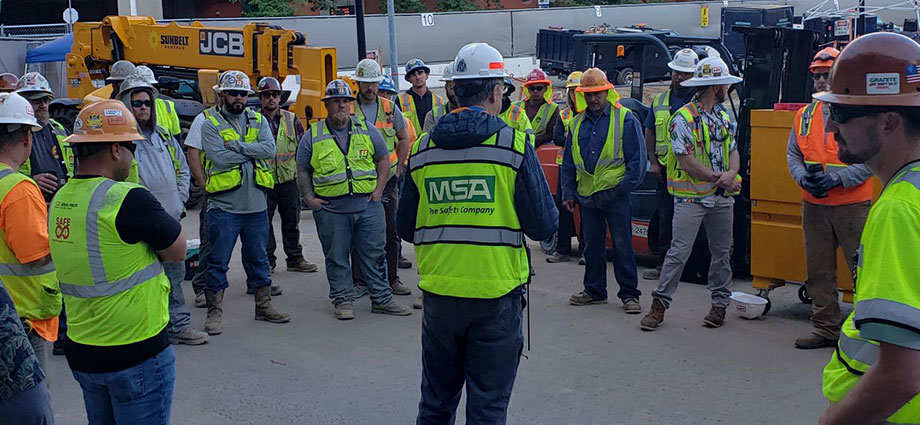
In your business, there is no room for haphazard operations, right? This is particularly important when it comes to workplace safety. We want to give our employees a safe environment in which to work. Of course, it’s also mandated by the Occupational Safety & Health Administration (OSHA).
In fact, the introduction to the publication OSHA 3012-06R 2017, Workers’ Rights states:
You have the right to a safe workplace. The Occupational Safety and Health Act of 1970 (OSH Act) was passed to prevent workers from being killed or otherwise harmed at work. The law requires employers to provide their employees with working conditions that are free of known dangers.
Under the Employer Responsibilities section of the same document, OSHA explains the requirements in more detail:
Employers have the responsibility to provide a safe workplace. Employers MUST provide their employees with a workplace that does not have serious hazards and must follow all OSHA safety and health standards. Employers must find and correct safety and health problems. OSHA further requires that employers must try to eliminate or reduce hazards first by making feasible changes in working conditions – switching to safer chemicals, enclosing processes to trap harmful fumes, or using ventilation systems to clean the air are examples of effective ways to get rid of or minimize risks – rather than just relying on personal protective equipment such as masks, gloves, or earplugs.
The employer responsibilities section forms the basis for this article topic: the hierarchy of controls as it pertains to hazard analysis and abatement.
What is the hierarchy of controls, and why is it important?
Interestingly, the word “hierarchy” originally pertained to the “pecking order” of angelic beings and church governance. In modern times, it has come to denote the order of importance in determining and implementing workplace processes or controls.
Using a hierarchy of controls keeps safety assessment for hazard abatement on track and effective. It’s used in the planning process to determine the most feasible and effective means of keeping workers safe from hazardous working conditions.
NIOSH (the National Institute for Occupational Safety and Health) is the United States federal agency responsible for conducting research and making recommendations for employee workplace safety. In the NIOSH national initiative, Prevention through Design (PtD), the hierarchy of controls is one of the strategies used.
We’ll delve deeper into the hierarchy in a minute. However, the five methods of control, from most effective to least effective, are:
- Elimination
- Substitution
- Engineering Controls
- Administrative Controls, and
- PPE (personal protective equipment)
It might seem that if the most effective method is elimination, using it is a no brainer. However, as we’ll discuss, it’s not always the most feasible. Using the hierarchy of control in hazard analysis and control planning is an important step in finding the best possible answer.
Here are brief rundowns of each control method.
Elimination and Substitution
These two control methods can be grouped together because of their similarity. Elimination means that you completely remove the hazard from the workplace. It’s the preferred way of controlling hazardous scenarios, particularly hazardous chemical processes.
Elimination of the hazard can sometimes be accomplished by physical changes. For example, if workers are at risk when making repairs on light overhead, bringing the light down to them eliminates the hazard.
However, it’s not always possible if the substance is integral to your operation. The next best option is substitution. In other words, replace the hazardous chemical, for instance, with one less hazardous. For example, you could replace organic solvents with a water-based detergent solution.
Sometimes, all that is needed is to substitute one form of the chemical for another. If dust or powder is an inhalation issue, substitute a more solid form, if possible.
Just make sure that if using substitution as the control that you aren’t trading one problem for another. Perform a risk assessment and evaluation before making the change.
Engineering Controls
Engineering controls involve separating or isolating the worker from the hazard. For example, loud machinery can be housed in a soundproof room, protecting the workers’ hearing.
In dusty environments, ventilation fans and filters remove airborne pollutants from the air around the workers.
In both of these instances, the hazard is still present, but the workers are protected from it by implementing effective engineering controls.
Administrative Controls
With the previous three controls — elimination, substitution, and engineering changes — little if any human interaction is necessary. However, with the last two, you introduce the human element. And with that, the potential for human error.
Administrative controls involve changes or improvements in procedures. This can include additional safety training to educate workers on safer ways to accomplish their tasks.
It may also include warning signs to point out hazards or safety tape to mark out safe working distances or walkways.
Of course, this places the responsibility for following instructions squarely on the shoulders of the workers involved. It does not eliminate the hazard or isolate the worker from it.
The training and other markers merely alert the worker to the potential hazard and how to avoid contact with it.
Personal Protective Equipment (PPE)
PPE is an important part of worker safety. Safety equipment helps shield the worker from the hazard. However, it relies on the worker to use it consistently and to use it properly.
“I’ll only be in there for a minute” is often used by a worker to beg off using some forms of PPE. However, dangerous activities don’t need that much time to cause damage.
As vital as properly chosen and properly donned PPE is to worker safety, safety equipment can’t insulate the wearer from every type of hazard. Additionally, the degree or severity of the hazard affects the PPE’s performance.
According to the nationally recognized head protection testing standard, ANSI/ISEA Z89.1-2014:
“Protective helmets reduce the amount of force from an impact blow but cannot provide complete head protection from severe impact and penetration.”
PPE is an important part of any safety program. But it should never be the sole control factor or means of protecting workers from on-the-job hazards.
Summing It All Up
Hazard analysis is an important part of keeping workers safe on the job. Additionally, it’s not just a one-time action. It’s an ongoing process. As workplaces change and processes evolve, further analysis must be done to ensure the safety of employees in potentially hazardous environments.
If possible, hazards should be eliminated, or substitutions made as the first step. This is best done in the workplace design phase but can be implemented at other times as well.
Engineering controls separate or isolate workers from hazards when elimination or substitution aren’t possible or feasible.
Finally, while administrative controls and PPE are important factors in any worker safety program, they should be considered as a last resort for helping to keep workers safe from harm.
Understand the hierarchy of controls and use it wisely to protect workers from harm. And remember … it’s not just a good idea.
It’s the law.

Additional Resources:
Centers for Disease Control and Prevention – Hierarchy of Controls
Occupational Safety and Health Administration – Hazard Prevention and Control