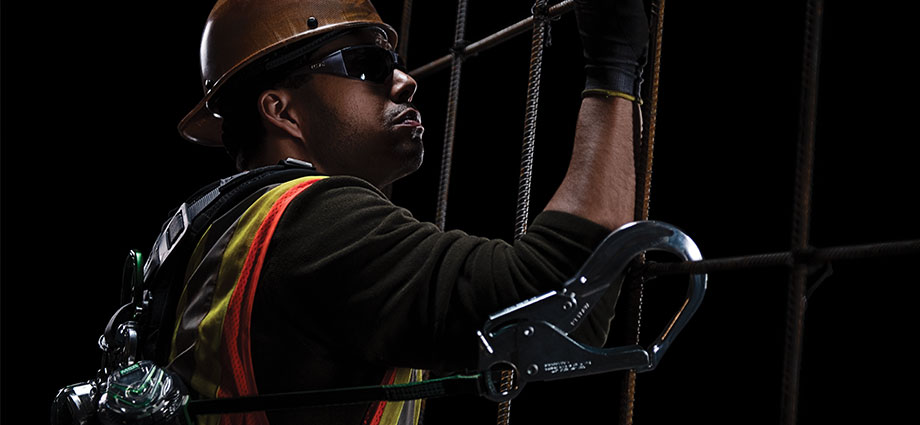
Falls from heights remain a leading cause of worker injuries and fatalities in the industry. Compliance standards require that the employer have a documented plan for fall protection and fall recovery.
There are some obvious reasons why you should have a documented plan:
- Economic incentives – keeping lost time and production downtime minimal
- Legal obligations – ensuring compliance and avoiding litigation
- Moral obligation – keeping employees safe is really just the right thing to do
To help create a safer working environment, some basic elements of a plan should include:
- Performing a hazard assessment
- Developing fall protection and fall recovery procedures
- Obtaining the technical equipment needed
- Using competent people to train workers and inspect equipment
- Ongoing training for the involved workers
It’s easy to realize that there are a lot of “moving parts” when protecting your team as they’re working at heights. A well-designed, documented fall-protection plan will help establish consistency.
As they say, if you do the same thing the same way over and over, you’ll get the same results each time. And when it comes to protecting your workers, that’s a good thing.
You may already have the first three elements covered. You’re providing a safe workplace. You’ve performed a thorough hazard assessment and developed a workable plan for fall protection and recovery. You have all the necessary equipment to make it work.
But let’s focus on the last two: competent people and ongoing training. Without these two vital elements, there’s a missing link in your chain of fall protection.
ANSI defines a “competent person” as:
An individual designated by the employer to be responsible for the immediate supervision, implementation and monitoring of the employer’s managed fall protection program who, through training and knowledge, is capable of identifying, evaluating and addressing existing and potential fall hazards, and who has the employer’s authority to take prompt corrective action with regard to such hazards.
Think of the “competent person” as the main manager for fall protection. They know the standards, equipment, hazards to be faced, and the overall fall protection program. The “Qualified Person”, by contrast, mainly deals with engineering issues. They help when there are technical issues that arise (such as analyzing a beam for strength or designing a complex fall arrest system) that the normal CP cannot handle. They, however, don’t really have responsibilities in running the program at all.
With that in mind, it’s important to use competent people to train and inspect
Competent trainers need to effectively communicate information to their students and peers.
A competent trainer may know and understand the standards involved but that’s not what they need to teach. They should communicate the hazards, not the standards. And they should be able to explain how workers can protect themselves.
Inspections should also be carried out on a regular basis. Those inspecting must be trained in how to recognize damaged equipment and what to do when they find it. Of course, workers should inspect their equipment every time they don it, even multiple times throughout their shift. But regular inspections by competent personnel is also an important step in thoroughly checking equipment. A second set of eyes always helps.
So, what should your employees be trained on when working at heights?
Fall protection training points
While it’s important for everyone to have an understanding of the standards, what employees really need is training on the hazards and how to protect themselves. This means the fall hazards they’ll encounter, and the fall protection systems and equipment they’ll use.
This includes:
- Scaffolding, ladders, and portable guardrails
- Designated hazard areas on roofs and other heights
- Safety nets, rope decent systems, and ladder safety systems
- And of course, personal fall protection equipment
The workers must be taught the ABCs of using fall protection equipment.
- A – Anchorage points and anchorage connectors
- B – Body wear, such as full-body harnesses and positioning equipment
- C – Connecting devices like shock absorbing lanyards and self-retracting lifelines.
Keep in mind that they need to know more than just how to self-inspect for wear and tear. For example, your team members must know how to don full-body harnesses properly.
Make sure you cover all the bases when developing your fall protection plan to include everything from identifying hazards to training your employees that work at heights.
You want to make sure they are protected at all times, whether there’s a fall event or not.