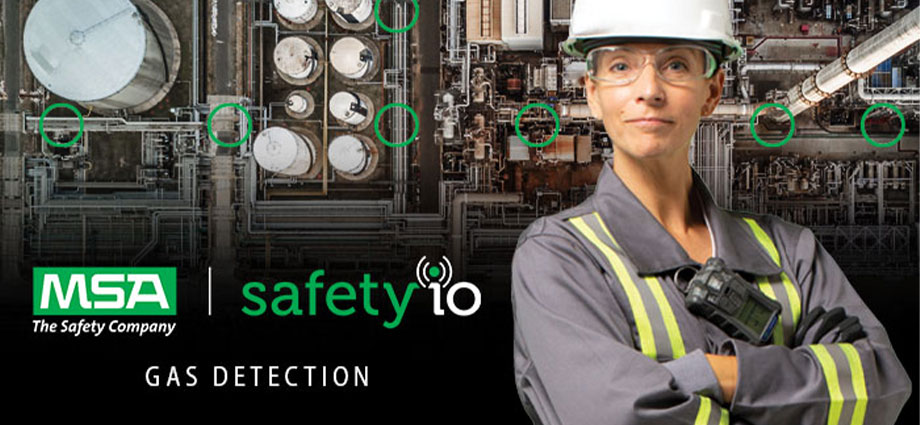
With a proactive approach to your gas detection program, you can increase worker accountability and device uptime while reducing safety management challenges. But, it’s tough to think ahead when you don’t have easy and functional data access.
If you spend hours retrieving incident reports or monitoring your portable gas detectors, it’s difficult to invest time into high-level tasks. Instead, set your devices for seamless connectivity, automated reporting and informed decision-making.
Going Digital With Gas Detection: A Proactive Approach to Safety Programs
Although continuous monitoring is essential, maintaining calibration records and compliance data is time-consuming. And managing your fleet of portable gas detectors gets more complex when your team in charge of safety can’t get into the office.
However, you can simplify matters by connecting your gas detectors to the MSA Grid cloud-based software. With your data secure in the cloud, it’s easier to remotely monitor gas readings and schedule maintenance. A flexible, user-friendly interface allows you to:
- Get real-time data from anywhere with an internet connection at any time.
- Oversee several sites and multiple gas detectors from one dashboard.
- Ensure automatic backups for OSHA-compliant record-keeping.
- Create and share reports even if you’re working from home.
Along with helping to creating a safer workplace, going digital helps you focus on achieving safety goals while taking a proactive approach to mitigating safety concerns.
Exploring the Benefits of a Cloud-Based Gas Detection Solution
Using a web-based service provides more than peace of mind. For example, the City of Asheville Water Resources Department attached its portable gas detectors to the MSA Grid and “reduced the time they spent managing detectors by 60%.” By connecting your MSA detection equipment to Grid services, you’ll:
- Improve your record-keeping process while reducing the time spent on administration.
- Prioritize actions using a daily email summary about your fleet’s status.
- Ensure accurate instrument maintenance records and strategically decommission devices for repair.
- Leverage data for thorough risk assessments using live and historical data.
- Develop better employee training programs using equipment usage information.
- Reduce downtime with gas detectors that are routinely calibrated and bump tested.
- Make informed decisions regardless of your location.
- Decrease costs related to record storage and IT support services.
How to Improve Your Safety Program
Keeping up with today’s complex worksites requires information at your fingertips. Moreover, it’s vital to automate data collection so you can have the means to improve safety awareness and outcomes. When it comes to connected worker safety, there are four mains pillars you should consider:
- Automated compliance management
- Incident prevention and management response
- Worker health and productivity
- Active safety monitoring
To take a deep dive into each of them, we recommend you listen to this podcast. Before you can develop these pillars, you want data access and availability that delivers clear, actionable insights.
Make Worksite Safety a Priority
Asking yourself what you can do right now? Well, gas detection plays a big role in your workers’ and worksites’ safety. A great way to improve your safety program is by getting your gas detectors to do more for you. With a connected gas detection program you can help improve visibility and compliance across your workers, worksites, and workflows, to ultimately drive safety outcomes. Learn more about your gas detection hardware and software options.
References