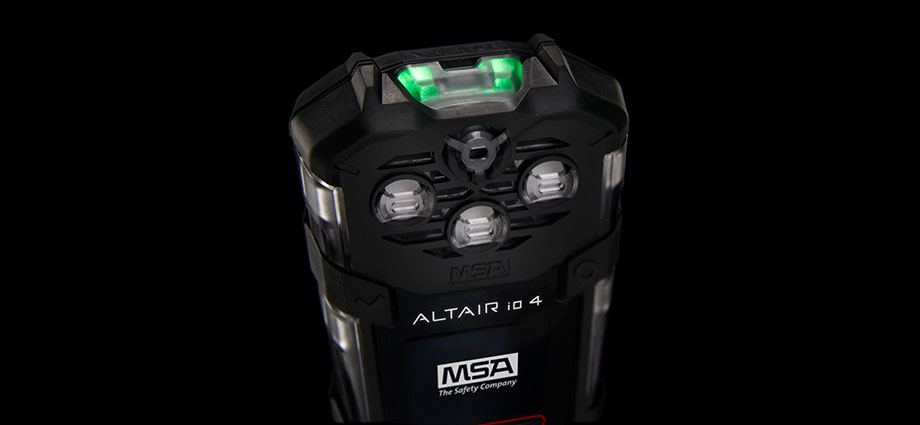
If you wait until an audit to look at your data logs, then you’re missing valuable opportunities to improve worker health and safety. From conducting risk assessments to driving employee accountability, gas detector’s data logs, when correctly analyzed, can provide valuable insights. Easily accessible data, brought together in the correct format, can empower your safety teams by enabling them to make better decisions.
Overcoming the Big Data Challenge
Can you monitor worker responses to alarms or quickly drum up data from a three-year-old incident report? Or are you flying blind? Reading your gas detector’s data log gives you the information you need to make informed preventative maintenance and employee behavior decisions.
With the ALTAIR io™ 4 Gas Detection Wearable and Grid cloud-based software, you get the data and insights across your workers, worksites, and workflows to help establish a proactive safety culture.
Use gas detection software services to automate compliance, reduce costs and create easy-to-understand reports. Safety managers rely on the Grid Fleet Manager and Grid Live Monitor for a variety of reasons, including:
- Device alert awareness and control: Get a real-time understanding of gas exposures and instrument readings while live monitoring employee location and movement with satellite and street views. You can also receive online alerts about man-down alarms, device concerns and panic button presses.
- Comprehensive field device manager: From employee contact details to battery, compliance and sensor life alerts, the Grid Live Manager puts all the data at your fingertips. Plus, you can access employee contact details and current detector readings.
- Information access: Along with a daily e-mail about your fleet’s status, you can access fleet information from anywhere with an internet connection. Easily share calibrations, detector records or alarm reports by downloading and sharing them at any time.
- Fleet compliance: Use your Grid Fleet Manager to determine what equipment is in use, who is using it, and which ones are available. You can also reduce downtime by decommissioning equipment requiring maintenance and ensure all gas detectors are bump tested, calibrated and that its sensors are functioning properly.
- Risk assessment: Identify hazards, understand root causes, and drive accountability using Grid Fleet Manager. Having this information helps you create safer processes and find training opportunities based on equipment usage information.
- Ensuring proper equipment use: Assign devices to specific workers and gain valuable insight into worker behaviors. Understand if workers are acknowledging alarms according to best practices or simply turning the devices off. Identify which users went to work without bump testing the instruments.
Worksite Safety: Prioritize a Comprehensive Approach
Many data log systems make it hard to access, review, analyze and share information. And if you’re examining data from multiple sites or hundreds of portable gas detectors, then it’s nearly impossible to get a comprehensive view.
Fortunately, Grid cloud-based software puts information at your fingertips regardless of your location. You can pull data logs from the cloud at any time and from anywhere. This gives you access to the information you need to oversee workers, correct behavior, and reinforce your safety-first message. When it comes to connected worker safety, there are four mains pillars you should consider:
Automated compliance management:
The process of inspecting gas detection devices, calibrating them and bump testing is time-consuming and complex. By adding connected technologies, you can automate the compliance process and free up time to focus on higher-level objectives. Put all information about your gas detectors in one spot in the cloud. Doing so helps you get a broad look at gas detector compliance data.
Incident prevention and management response:
The goal is to prevent every incident but to get there, you want access to data analytics. Connecting to gas detectors for real-time incident reporting and increased worksite visibility helps you follow up and thoroughly document any problem. Use a comprehensive field device manager for current detector readings and alarm notifications to act quickly.
Worker health and productivity:
Connected worker safety means figuring out how technologies, like connected gas detectors, can help protect teams and safely boost productivity rates. Develop insights into worker safety by reviewing how and when devices are used. Use this information to identify training opportunities.
Active safety monitoring:
By giving safety managers access to data from anywhere with an internet connection, they can stay on top of safety activities without walking through the facility daily. From afar, safety managers can see employees’ locations using street and satellite views while getting real-time notifications of gas exposures and instrument readings.
Take Action to Improve Workplace Safety
Your gas detection data logs are crucial to fleet compliance. Yet, maintaining accurate records is only one element of your safety program. Use data logs to develop insights, optimize worksite safety and achieve successful outcomes. Learn more about the ALTAIR io 4 device and Grid software by watching this on-demand video demo.