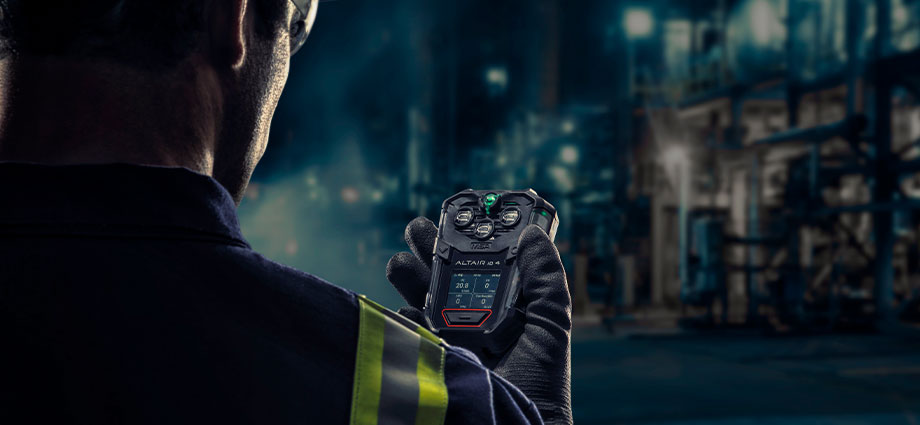
We live in a connected world, where connected devices have helped to create “smarter” experiences in our day-to-day lives.
This connectivity has the potential to truly transform how we work, too.
In fact, industries including oil & gas, chemical production, and construction are leading the way in terms of adopting connected worker technologies within the next two decades.1
But what role does PPE play in driving this connected work transformation?
With a reported 2.8 million workplace injuries and illness as recently as 20192, and an estimated 80 – 90% of those attributed to human error3, PPE must not only help keep workers safe, but also provide the data and insights that can help organizations implement connected, adaptive safety cultures.
The Challenge with Traditional PPE
Despite the millions of workplace injuries, the costs associated with them, and productivity lost because of them, PPE has traditionally remained in the dark, rarely incorporating any technology solution or component that could help to prevent these issues. That is why the future of PPE lies in connected devices that you can rely on to provide the data and insights to help improve worker and worksite safety. This includes facilitating adequate maintenance programs, keeping inspections and records up-to-date, and identifying issues before they pose a risk to workplace safety.
The future of PPE is connected devices.
But What Does “Connected” Mean?
While traditional PPE protects the wearer, it does not have the capability to enable real-time visibility across workers and worksites, or provide the data to help influence ongoing worker behavior based on insights and trends. Also, manual recordkeeping and maintenance processes can be subject to inconsistent and incomplete information as the demands on workers and safety managers increase.
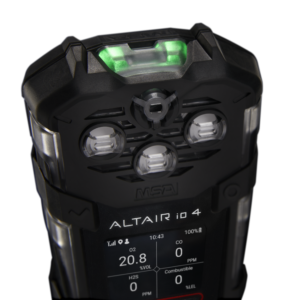
The term “connected” not only means a connected device – one that comes with out-of-the-box cellular connectivity to the cloud – but also a comprehensive solution inclusive of hardware, connectivity, and software. It’s not necessarily enough to simply have cellular connectivity; hardware should also be connected to software, so that connectivity can provide the real-time data and insights to help drive adaptable, proactive safety programs.
This connectivity transforms hardware from traditional PPE to a technology-based, future-forward solution. Successful integration of this advanced technology requires that not only are devices smarter, but they continue to perform with the durability and functionality to maintain their mission to help protect the worker.
Benefits of Connected Solutions
Utilizing technology in the workplace can not only help to improve the health and safety of employees, but it can also help make companies more adaptive and efficient – connecting workers, worksite, and workflows.
Integrating a connected PPE solution can help organizations to:
- Enable proactive, real-time safety monitoring for enhanced awareness, visibility and informed decision-making
- Streamline compliance, allowing safety teams to be more proactive towards maintenance concerns and worker behavior
- Reduce the risk of incidents resulting from human-error
- Support increased productivity by saving time and enabling accuracy while simplifying the management of the overall safety program
What is The First Step to Start Using Connected PPE?
Building a connected safety program doesn’t happen overnight. But one step forward is all it takes to start– and implementing hardware might just be the easiest place to start. With the ALTAIR io™ 4 Gas Detection Wearable, part of the Connected Work Platform, you get the rugged durability you expect from an MSA gas detector, with connectivity built-in from day one – and immediate integration with a connected solution.
Learn more about the ALTAIR io 4 and Connected Work Platform here.
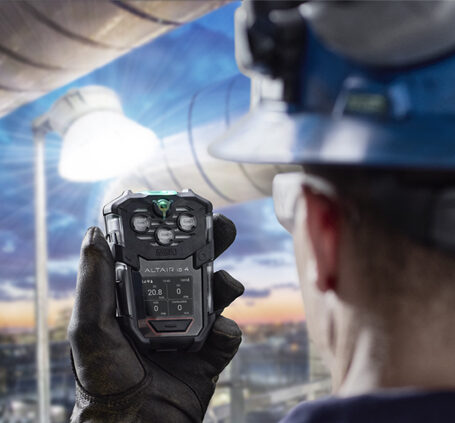
References:
1 https://www.visualcapitalist.com/connected-workers-digital-transformation-future/