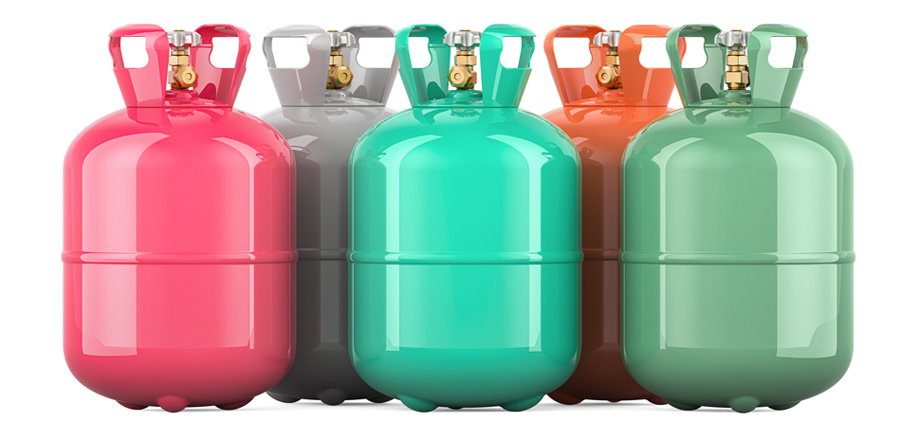
What is the AIM Act?
The American Innovation and Manufacturing Act (AIM Act) was signed into law December 27, 2020. Seeking to reduce the production and usage of hydrofluorocarbons (HFCs), the act gives the Environmental Protection Agency (EPA) the authority to phase out a large percentage of HFC usage in the United States by 2036. The goal of the act is to bring the US in line with the Kigali Amendment of the Montreal Protocol, an international agreement aiming to reduce HFC emissions and environmental impact globally.
What are Hydrofluorocarbons and why is reducing emissions a priority?
According to the EPA, hydrofluorocarbons are a type of man-made fluorinated gas that has a very high global warming potential (GWP). The use of hydrofluorocarbon gas has been trending upward in recent decades as a popular substitute for ozone-depleting substances (ODS). Similar to what is taking place with HFCs, the use of ODSs was phased down until they were ultimately banned, helping contribute to the increased usage of HFCs. Today, HFCs are commonly used as the primary refrigerants in modern refrigeration and air conditioning applications. The EPA reports HFCs are also used in fire suppression, solvents, foam-blowing agents, and aerosols. HFCs are not easily removed from the atmosphere. The EPA notes that many fluorinated gases remain in the atmosphere until they break down in the upper atmosphere due to sunlight exposure. Their long life, combined with high GWP, makes fluorinated gases among the most potent greenhouse gases released into the atmosphere by human activities.
What is global warming potential?
The EPA explains global warming potential as a unit of measurement intended to compare the holistic global warming effect of different greenhouse gases. The unit of measure is derived by comparing the warming effects of a greenhouse gas with carbon dioxide (CO2). The measurement examines how much energy would be absorbed over a period of time by the release of 1 ton of any gas into the atmosphere compared to 1 ton of CO2 gas. The higher the number, the greater the warming effect the gas would have on the Earth compared to CO2 over the same time period.
Because carbon dioxide is the reference gas, it has a global warming potential of 1. According to the EPA, fluorinated gases can have GWPs in the thousands to tens of thousands. For hydrofluorocarbon gas, the EPA lists the global warming potential as up to 12,400 over 100 years, with a potential lifetime in the atmosphere of up to 270 years.
What are the focal points of The AIM Act?
With such high potential to warm the atmosphere, the overall goal of the AIM Act is to reduce the usage of HFCs through three focal points:
- A phasedown of the production and consumption of HFCs
- A transition to different technologies
- Better management of applications that continue using HFCs
1. Production and Consumption Phasedown
A phasedown of the supply of hydrofluorocarbons is already underway in the United States. The first step down began in 2022 with supply of HFCs being cut by 10%. Another 30% drop in the supply has been implemented for 2024, bringing the total supply phasedown to 40% compared to pre-AIM Act baseline levels. Another 30% drop is scheduled for 2029, then another 10% drop occurs in 2034, followed by the final scheduled drop of an additional 5% by 2036. In total, an 85% reduction in the baseline supply of HFCs is scheduled to occur by 2036.
As supply drops, it is projected that the cost of the refrigerant will go up and continue to rise over time as supply is further restricted. This projected increase in refrigerant cost makes having an aggressive leak detection strategy important to the bottom line. The higher cost means replenishing charge of HFC refrigerants from a system with a leak will become a more impactful expense to the system owner than it has been in previous years. The earlier that the detection system can identify a leak, the higher the likelihood a leak can be stopped when minimal gas is released. In this manner, refrigerant leak detection becomes impactful for both environmental and economic reasons.
2. Transition to Different Technologies
Subsection (i) of the U.S. EPA AIM Act regulations focuses on reducing the demand for HFCs. This is done by establishing limits, based on global warming potential, of refrigerants used in the manufacturing of HVAC and Refrigeration products and equipment. Compliance with these conditions and restrictions is expected to drive significant change in the HVAC-R industry. The new restrictions are slated to begin January 1, 2025, with additional restrictions for specific industries set to begin in 2026, 2027, and 2028. Below is a list of some application-specific restrictions, based on global warming potential, taking effect through the late 2020s:
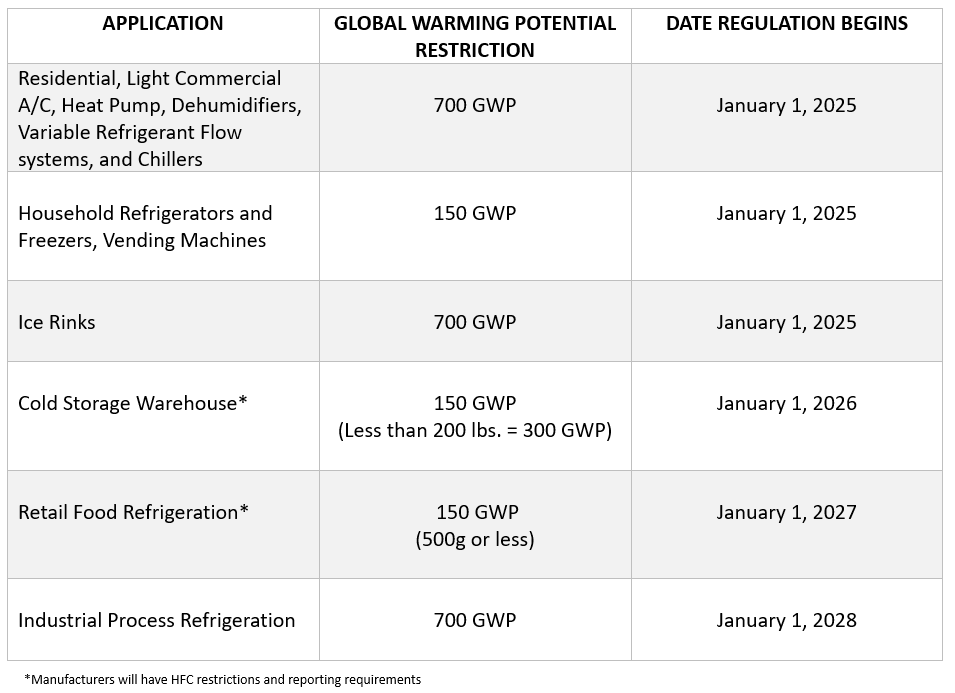
3. Refrigerant Management
Subsection (h) of the AIM Act establishes regulations for HFCs and identifies acceptable substitute gases to maximize the reclaiming of used gases and limit leaks from equipment. The regulation also aims to enhance the safety of technicians and consumers. This area of the AIM Act is currently still being finalized. A regulation proposal was released October 6, 2023 with a finalized version expected sometime in 2024.
One of the primary focuses of subsection (h) will be the required use of Automatic Leak Detection (ALD) systems. The EPA will set requirements for low-level leak detection in new or existing systems, with the exact requirements expected to be finalized in the 2024 rule. Other expected regulations are expected in the following areas:
- Leak repair of appliances containing HFCs
- Reclamation standards
- Use of reclaimed HFCs in certain refrigeration, air conditioning, and heat pump applications
- Container tracking of HFCs
- Recordkeeping, reporting and labeling of HFCs
- Recovery of HFCs from disposable cylinders
- Service repair, disposal, or installation of HFC-containing fire suppression equipment
How can MSA help businesses prepare for automatic leak detection requirements?
With over 30 years helping safeguard people, places, and the planet, MSA offers a suite of products that can help comply with future HFC regulation standards and enhance refrigerant leak detection and management programs. Some MSA products are considered direct detection ALD solutions due to their ability to determine gas concentration with direct exposure to a sensing element. Within the direct detection classification, there are two different types of sensing methods used:, aspirated refrigerant monitoring systems and diffusion point detectors .
What is an aspirated refrigerant monitoring system for refrigerant leak detection?
An aspirated refrigerant monitoring system pulls in samples for analysis from areas where leaks are most likely to occur. This type of sensor offers detection for low-level leaks, capable of Minimum Detectable Levels (MDL) as low as 1 ppm. Sample points are strategically placed near each leak-prone area of HVAC-R equipment to catch leaks as early as possible. The continuously active sample cycle, combined with the low-level detection limits offered by the infrared sensing bench, make aspirated systems highly valuable for emissions reduction through early leak detection.
What is a diffusion point detector for refrigerant leak detection?
A diffusion sensor requires the gas to disperse into the air and reach a sensor for a leak to be detected. Additionally, the refrigerant gas will dilute into the greater occupied space and a leak may not be detected until the full room has reached a threshold concentration level. A diffusion system is unlikely to detect small leaks and may struggle with moderate leaks. High-level, or gross refrigerant leaks are likely to be detected, though leaks of that magnitude are considered uncommon. Diffusion-based systems typically have a MDL of around 200 PPM and are key pieces of equipment for safety of personnel in a mechanical or rack room .
MSA products supporting automatic leak detection requirements
The MSA Single-Zone Refrigerant Monitor, the MSA Bacharach Multi-Zone Gas Monitor, and the MSA Chillgard® 5000 Refrigerant Leak Monitor all meet the currently proposed regulatory leak detection requirements of subsection (h) of the AIM Act. All three systems utilize aspirated sensing principles for detection and can detect leaked gases as low as 1 ppm, which is considered very early detection for the average leak rate. These detection systems are capable of monitoring up to 16-zones, expandable to up to 48 sample points, for more than 60 different refrigerants with a single monitor and centralized sensing bench.
These MSA products are compatible with the MSA Bacharach award-winning Parasense Refrigerant Tracking & Compliance Software, offering industry-leading refrigerant management and tracking tools to help users reduce operating costs, gain regulatory compliance, and become leaders in sustainability and efficiency.
MSA products supporting leak inspection requirements
The MSA Bacharach PGM-IR Portable Refrigerant Monitor meets the currently proposed regulatory leak inspection requirements of subsection (h) of the AIM Act. This sensor is portable and can be used to inspect areas and pinpoint exact locations where leaks are likely to occur, with a MDL as low as 1 ppm. Changes in temperature or humidity do not impact the sensor, and it is not prone to false alarms caused by the presence of other gases.
The unit features a gas library of over 60+ refrigerants, including HFCs, similar to the Multi-Zone Refrigerant Monitor. The PGM-IR portable monitor also features an integrated charcoal purge filter that allows users to perform inspections in contaminated spaces without leaving to re-zero the monitor in fresh air.
How can automatic leak detectors save users money?
In addition to maintaining compliance and avoiding potential fees for being non-compliant, ALDs can save users money through the benefits of early leak detection. Early detection of leaks allows for a fast response, preventing further loss of refrigerant gases and timely deployment of a technician to repair the leak. Utilizing ALD systems will become even more of a cost-saving tool as HFC recharges become more expensive with a decrease in the supply of the gas.
Consider the following hypothetical leak scenario and the associated costs for recharging the system:
According to an EPA document, a typical grocery store maintains a 4000-pound refrigerant system with an average loss of around 25% of the refrigerant yearly. That translates to a loss of around 1000 pounds of refrigerant each year. Based on today’s cost of roughly $24/pound for R-404A refrigerant, the recharge cost would be around $30k when you factor in markups and labor.
As requirements of the AIM Act are implemented, supply of HFC refrigerants will drop and cost is expected to rise. MSA estimates the cost of R-404A refrigerant will increase by 10% to 30% by 2027. The cost to recharge refrigerant systems will increase.
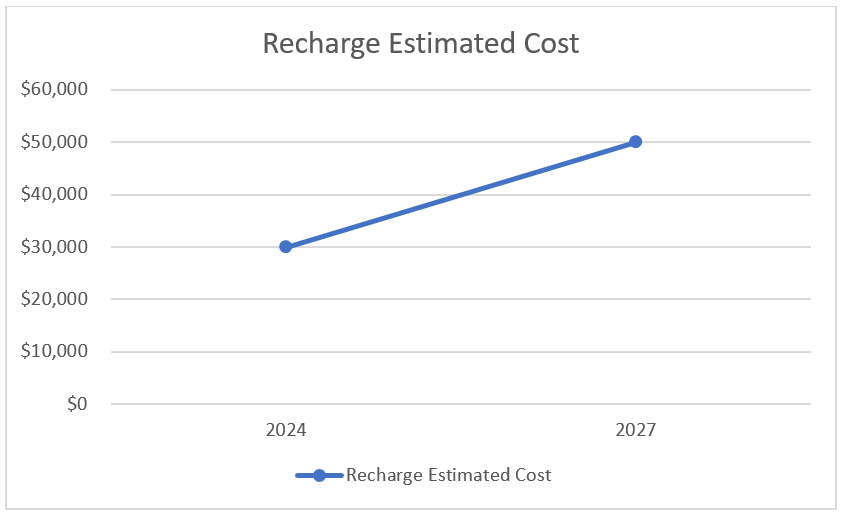
By MSA estimations, cost to recharge the same system that would cost around $30k today could jump as much as $50k to $100K by 2027. Without doing something to mitigate refrigerant loss, such as installing an automatic leak detection system to catch leaks early so user can repair leaks early, users of these systems will likely spend much more for a recharge.
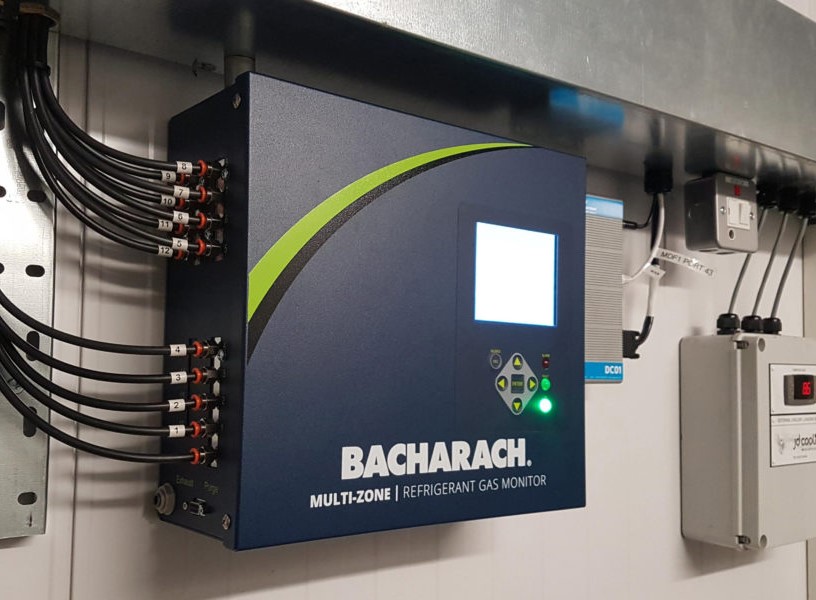
Get a jump start on complying with upcoming regulations and experience the cost-saving perks of early refrigerant leak detection.
Explore MSA products for monitoring refrigeration systems today!
LEARN MORE NOW