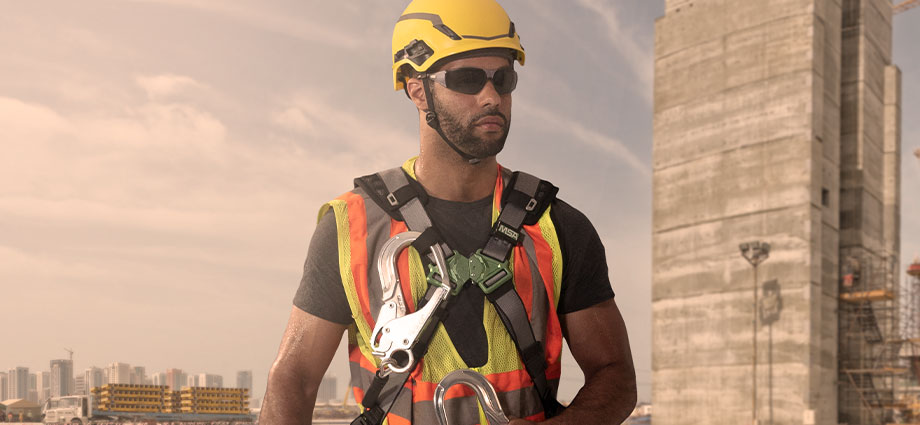
In a recent article, we discussed the “expiration date” for hard hats. Technically, they don’t have a standards-defined EOL (end of life) date or definitive shelf life. After all, we’re not talking about a food item or other perishables. That said, most manufacturers do have guidelines for the inspection and replacement of some components based on the manufacture date and/or the date of first use.
But what about fall protection harnesses?
Is there a fall protection harness expiration date, beyond which they’re deemed unusable?
The answer is both yes … and no. Here’s why.
Who Defines a Fall Protection Harness’s Expiration Date or End Of Life?
There is no such thing as a predetermined or mandated expiration date on fall protection harnesses. Neither OSHA nor ANSI have current codes or standards that set a specific time period for taking a harness out of service. Even most manufacturers will not suggest how long a harness will last.
In fact, the only person who can truly determine when a harness is due for removal is you or your competent, trained inspector. More important than who determines its end of life is what determines it.
The Potential Problem With a Mandated Expiration Date
You might think that having a mandated expiration date for a fall protection harness would be a good thing. However, it could have some adverse effects.
For example, it could lull the wearer or safety professional into a false sense of security.
“My harness is only a year old, so I’m confident I’m adequately protected. This harness still has four years of use left in it.”
See the problem?
It’s possible to become complacent, taking for granted that the harness will perform properly if and when needed. The wearer might skip inspecting for defects each time the harness is used. Additionally, a false sense of security may cause the recommended, competent person annual inspection to be put off or even skipped.
Things That Affect a Fall Protection Harness’s Useful Lifespan
As with any PPE (personal protective equipment), a full body fall protection harness must be cared for and used properly. Some of the things that affect them adversely are:
- Snagging on protruding objects that might cause tears to the harness’s fabric or stitching. This can cause a weak spot that could fail during a fall arrest.
- Coating or saturation of paints and other chemicals can weaken the synthetic materials used in the webbing construction. Remove these materials as soon as possible, using the manufacturer’s guidelines to avoid further deterioration.
- Excessive exposure to UV rays or sunlight may cause deterioration or weakening of synthetic fibers. When the harness is not in use, store it away from sunlight.
- Exposure to caustics and acids may deteriorate the metal components, such as the D-ring and buckles. Clean these items as soon as possible using approved methods.
- Improper storage methods can damage the harness. The harness should be stored in a hanging position so that the webbing can “relax.” Hang the harness by the D-ring, not the webbing.
- Any harness subjected to a fall arrest must be taken out of service immediately. Do not use the harness after the impact event. It must be labeled as unusable and removed from service until destroyed.
The Only Way to Determine a Harness’s Usability is Through Routine Inspection
Checking the harness carefully for damage is the only reliable way to determine its condition. This includes a pre-use check by the wearer before donning the equipment and the periodic inspection by a qualified, competent inspector.
A competent inspector will be trained in proper inspection procedures and should document each harness’s inspection with a log sheet. While the pre-use inspection is necessary, the closer look an inspector gives the equipment ensures the harness is inspected properly.
ANSI recommends that formal inspections should be done at intervals of no more than six months. An inspector should not be the person wearing that particular harness. The log sheet used should match the exact harness if possible.
We advise that a harness that has not been formally inspected within that six month period be taken out of service and tagged unusable until a formal inspection is completed, including documentation.
A Five Step Procedure for Harness Inspection
Here are the five steps you should follow in doing a formal inspection.
-
Inspect all webbing and stitching
You’re checking for cuts, fraying, pulled or broken threads, abrasions, excessive wear, altered or missing straps, burns, UV damage, and heat and chemical exposures. Starting at one end of a webbing length, grasp the webbing with hands eight inches apart and flex the fabric. This can expose any defects not seen with the webbing in a straight alignment.
-
Inspect all metal or plastic components of the harness
All harness buckles should work freely, engaging and disengaging fully and smoothly. Depending on the model harness you use, make sure each type of buckle, including a quick connect buckle, is functioning properly.
Look for deformation, crack, corrosion, deep pitting or burrs, sharp edges, nicks or cuts, exposure to excessive heat or chemicals, and any other damage. Missing, loose or improperly working parts should be noted. This should include both metal and plastic components.
-
Inspect all load indicators
Load indicators are sections of the harness webbing that are folded over and stitched securely. Ripped stitching, even if only partially separated, is an indicator that the harness has been subjected to a fall and is no longer providing adequate protection. Remove the harness from service immediately. Mark it as unusable and remove from service until destroyed.
-
Inspect all labels
To fully pass inspection, labels must be present and readable. Make sure the unique identifier for the harness is legible so that it can be marked properly on the log sheet.
-
Complete all inspection documentation
A formal inspection is not done until the paper work is filled out. Create a log sheet if necessary, covering all the check points for the harness you use.
Many suppliers, like MSA Safety, can furnish you with a complete, fully itemized inspection log for each model they sell. Your log should have a place to enter condition codes, overall assessment scores, and room for the inspector to make comments.
Keep in mind that an assessment doesn’t work on a sliding scale. The component, no matter what it is, gets a Pass or Fail rating. There is no in-between.
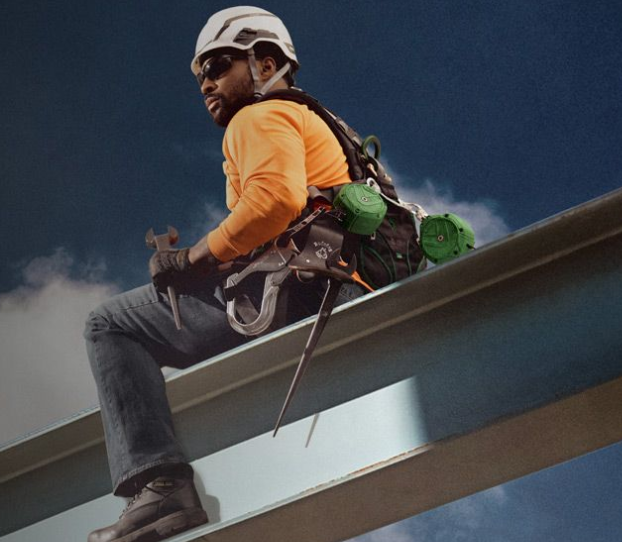
Experience the Standard in Fall Protection with MSA PPE
Experience the Standard in Fall Protection with MSA PPE. Learn more about the Dare to Compare product trial program:
Learn More