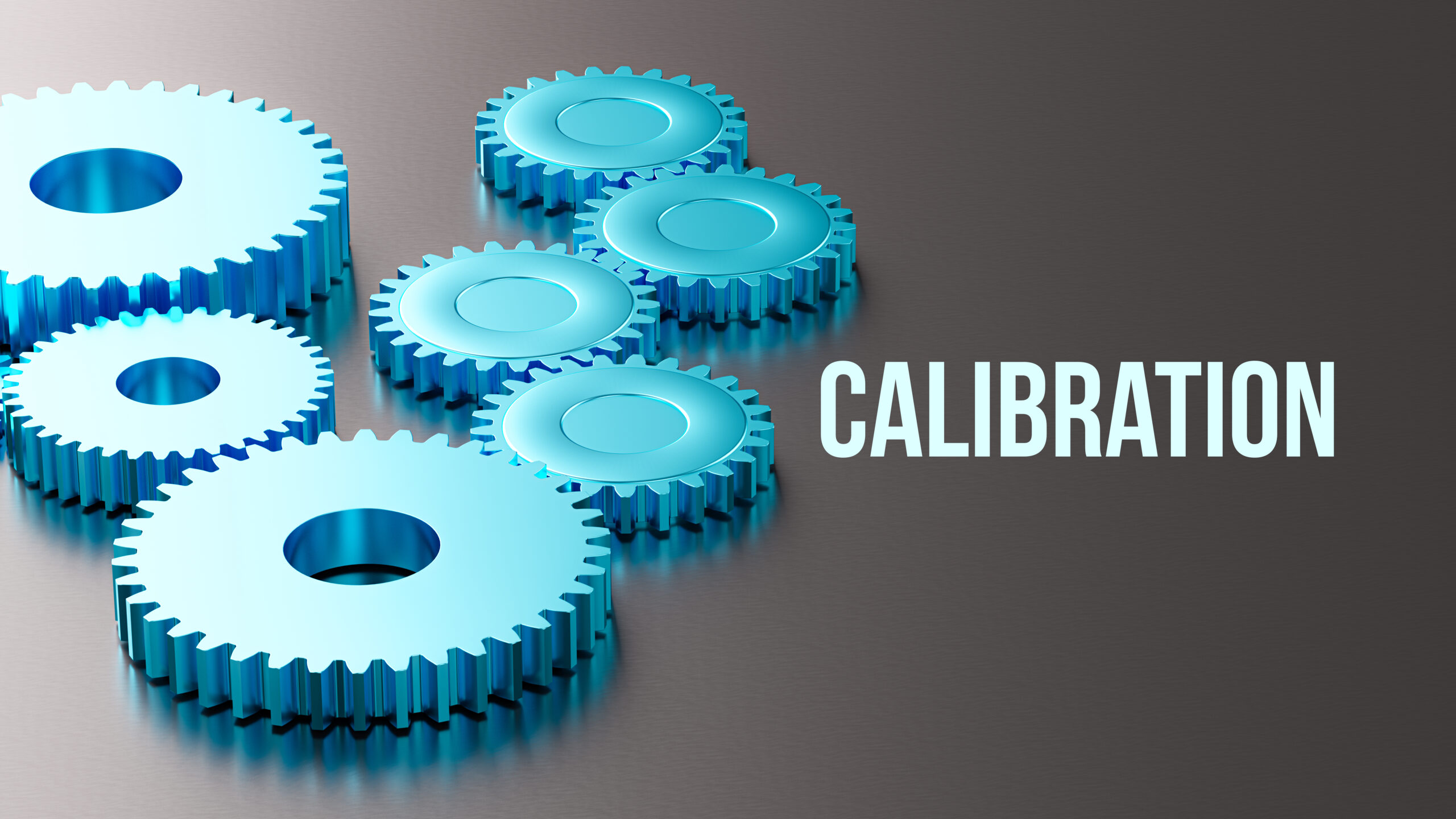
Calibration drift refers to the gradual shift in the accuracy and reliability of a detector’s measurement of gas concentrations over time. Fixed gas detectors play a pivotal role in safety, as they monitor the presence of hazardous gases in various environments, including industrial settings, laboratories, and confined spaces. Calibration is a critical aspect of ensuring that a gas detector functions correctly and provides accurate readings.
Several factors specific to gas detectors can contribute to calibration drift:
- Sensor Degradation: Gas detectors typically employ sensors that are sensitive to specific gases. Over time, these sensors can degrade or become less responsive, leading to inaccurate gas concentration readings.
- Contaminants: Exposure to certain gases or contaminants in the environment can affect the sensors’ performance. This can result in drift as the sensors’ responses to target gases are altered.
- Environmental Conditions: Temperature, humidity, and pressure can influence the accuracy of gas detectors. Fluctuations in these conditions can lead to shifts in calibration.
- Gas Exposure: The detector’s exposure to high concentrations of the target gas or other interfering gases can impact its calibration. Extended exposure to high gas levels can damage the sensors or cause them to drift.
- Wear and Tear: The physical components of a gas detector, such as the housing, filters, and connectors, can deteriorate over time. This wear and tear can affect the instrument’s overall performance and calibration.
To address calibration drift, routine calibration and maintenance are essential for gas detectors. This involves:
- Regular Calibration Checks: Gas detectors should be calibrated at specified intervals, typically in accordance with manufacturer recommendations and industry standards. During calibration, the detector is exposed to known concentrations of gases to ensure its measurements are accurate.
- Sensor Replacement: If sensors degrade significantly or no longer provide reliable readings, they may need to be replaced. Sensor replacement is a common maintenance task to combat calibration drift.
- Environmental Monitoring: Monitoring and controlling the environmental conditions in which the gas detector operates can help minimize drift. This may involve placing the detector in a controlled environment or implementing compensation algorithms to account for environmental effects.
- Proper Handling: Ensuring that the gas detector is used correctly and not exposed to excessive gas concentrations can help prolong its accuracy.
- Record Keeping: Maintaining detailed records of calibration dates and results is crucial for tracking the instrument’s performance over time and identifying trends in calibration drift.
MSA’s TruCal® sensors represent a major advancement in combating calibration drift for hydrogen sulfide (H2S) and carbon monoxide (CO) gases. These sensors, built with advanced materials and technology, enhance stability and reliability by minimizing the effects of environmental factors and gas exposure. TruCal eliminates the need for regularly scheduled calibrations by using Adaptive Environmental Compensation (AEC).
AEC tests the sensor every six hours and adjusts sensor response to account for changes in sensor response due to environmental conditions and sensor degradation. Sensors will perform within stated performance specification for up to two years without manual calibration. This translates to longer sensor life and less frequent calibration needs, saving users valuable time and resources.
MSA’s dedication to advancing sensor technology underscores our commitment to delivering accurate and safe gas detection solutions, even in the presence of calibration drift challenges. Download our TruCal whitepaper to learn more about this breakthrough technology.