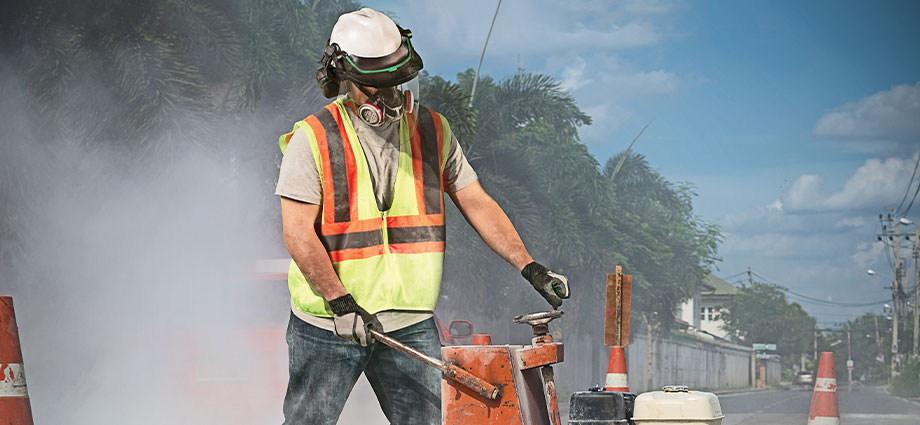
In this article, we’ll discuss three important points:
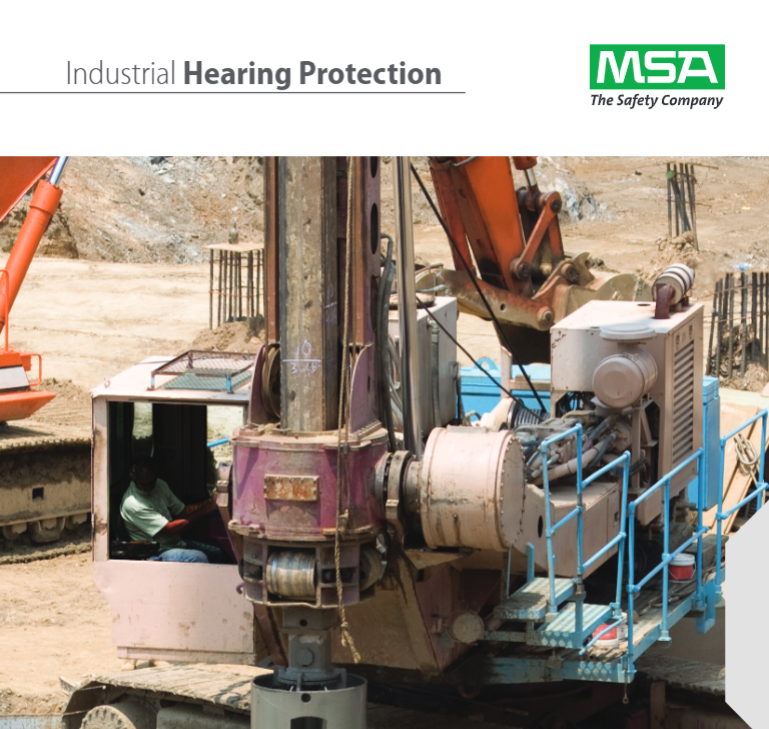
For more information, download our Industrial Hearing Protection brochure.
The potential dangers of noise in the workplace
An estimated 22 million workers are exposed to potentially damaging workplace noise. This fact was reported in a U.S. Department of Labor Occupational Safety and Health Administration paper entitled “Occupational Noise Exposure.”
According to the Centers for Disease Control and Prevention (CDC), occupational hearing loss is one of the most common work-related illnesses in the United States.
What makes hearing loss particularly insidious is that it’s often painless, gradual, and progressive. Usually there are no visible signs of injury. That means the almost 24 percent of U.S. workers affected by hearing loss… never heard it coming.
The importance of hearing protection
Prolonged or excessive noise exposure may damage nerve endings in the inner ear and present long-term challenges both on and off the job.
This potentially permanent and lifelong problem may affect workers’ ability to perform even daily, mundane tasks.
Workers in high-decibel level areas are affected most. That’s one reason OSHA (the Occupational Safety and Health Administration) requires employers to conduct annual hearing tests for these team members.
It begins with a baseline test to establish hearing acuity. This usually happens with new hires, or when an employee transfers to a job with high noise levels.
Additional tests help determine the effectiveness of the company’s hearing protection program, allowing them to make changes if necessary.
It also includes measuring workplace noise levels annually so that appropriate hearing protection procedures or equipment are planned for and implemented. Decibel levels are determined by using a TWA (time weighted average) method.
Hearing tests alone won’t alleviate the problem. But they can help determine the controls and PPE that help prevent this debilitating occupational hazard.
Some dangerous noise levels can be engineered out. Engineering controls can prove an effective line of defense. They include physical measures such as redesigning equipment or constructing barriers to block the noise. Unfortunately, not every noise hazard can be eliminated that way.
In those cases, personal protective equipment for safeguarding hearing becomes essential.
Hearing protection devices (HPDs) must be properly selected, worn, and maintained.
HPDs aren’t one-size-fits-all by any means. Each worker is different, as well as the workplace environments.
Choosing the right HPD for the job is based on several factors:
- Decibel level of the work area to determine the NRR (noise reduction rating) of the device used, also called attenuation levels
- Worker comfort
- The ability of the worker to use and maintain the HPD on his/her own (the product should be simple to use and unobtrusive
- Other options such as enhanced worker-to-worker communication
Monitoring and recording work areas help determine the suitable HPDs for the area. And the annual monitoring informs the employer when a change in process affects their hearing conservation program.
Of course, hearing protection that isn’t worn isn’t effective. Worker comfort has much to do with how often HPDs are used.
In a report published by US National Library of Medicine, National Institutes of Health, researchers found a link between comfort and the likelihood of consistent and correct HPD use.
The study concluded that “hearing protection must be selected with as much attention to comfort, convenience, and communication as to attenuation characteristics.”
In other words, hearing protection that’s comfortable and easy to use is more likely to be used. If not… it could be a roll of the dice.
The types of hearing protection available
The two basic types of hearing protection devices are ear plugs and earmuffs.
Earplugs are inexpensive and relatively simple. Made of soft foam or silicone, they simply insert into the ear canal. However, users should be trained in properly placing them.
For some users, they may take time getting used to.
Foam plugs are normally discarded after a single use. Silicone plugs may be used multiple times as long as they’re cleaned and disinfected.
They must also be inspected frequently for damage or wear. If damaged, discard them.
Earmuffs are pricier, but have benefits that offset the cost. Training is minimal. Most people already use headsets and headphones for music and other activities. That familiarity makes ear muffs a natural fit.
They can also prove more effective in high-noise environments where extended use is necessary. And they’re more visible, making it easier to monitor their use.
Earmuff HPDs have a much longer lifecycle and many parts, such as the foam cushions and inserts, are replaceable. They can be purchased with headbands for over the head applications.
Many models can be attached to a worker’s hard hat. When not needed, they can be swung out of the way.
A major benefit to hard hat mounted earmuffs is that they’re always with the worker. This often leads to increased HPD use, a major factor in hearing protection.
Final thoughts on hearing conservation
Hearing protection isn’t just a good idea… it’s an OSHA regulated practice when in environments where necessary. It’s estimated that U.S. businesses pay more than $1.5 million in penalties for not implementing or following OSHA’s hearing conservation program.
For more information, download our brochure, Industrial Hearing Protection. It provides useful information on choosing the right hearing protection for your workers, along with valuable charts to insure you have the correct HPDs for all your workers’ activities.