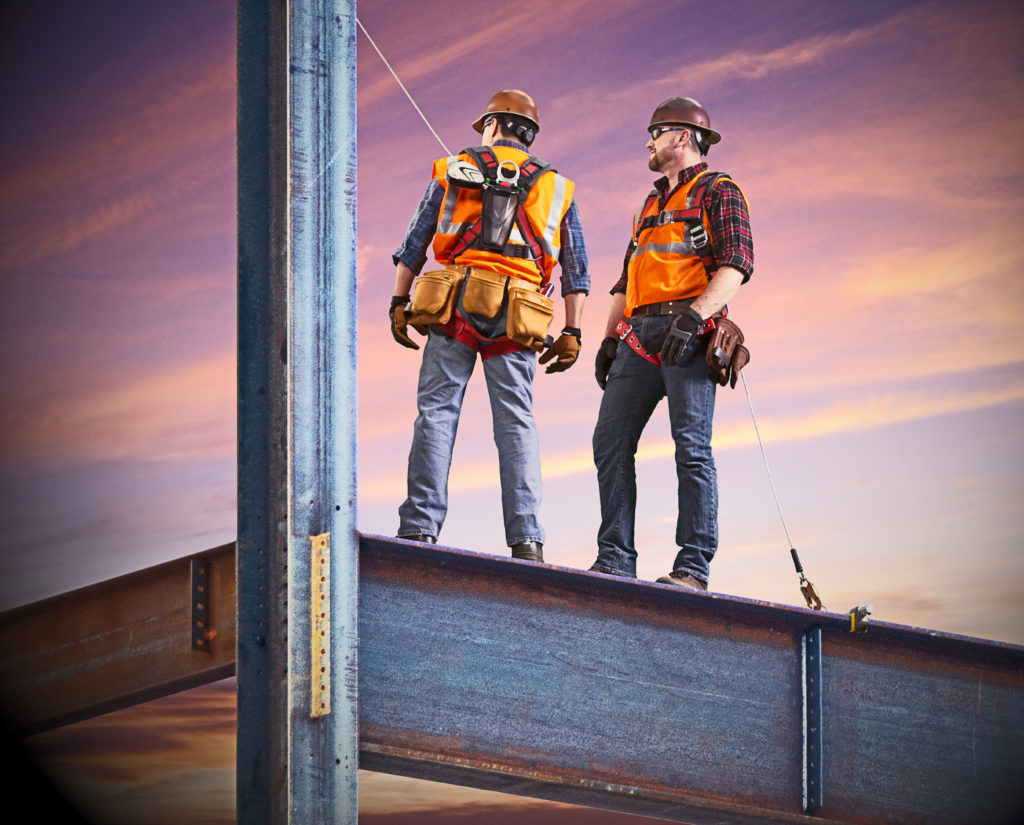
It’s crucial that employees have equipment to help protect against serious injury and death when working at heights. Fall protection is a vital part of construction, industrial maintenance, and related fields and industries.
Even though providing fall protection equipment is required by OSHA regs, as a safety professional, your commitment goes deeper than just compliance. You want your team members to go home each night to their families.
Here are some sobering statistics for the construction industry.
In 2016, OSHA (the Occupational Safety and Health Administration) reported that out of 4,693 deaths in private industry, 991 or over 21% were in construction. In other words … one in five worker fatalities.
Of those 991 construction fatalities, 384 or over a third of them were the result of falls. What’s even more disturbing is that of the top 10 most frequently cited OSHA standards violated in 2017, fall protection in construction continues to be number one. We need to improve those statistics.
One of the most talked about topics in fall protection is the “leading edge” concept and it’s been the subject of regulatory and standards organizations for the past several years.
In this article, we’ll discuss:
- How “leading edge” is defined by OSHA
- How it affects the design of fall protection equipment
- What to look for when choosing SRLs (self-retracting lanyards) for leading edge applications
At the end, I’d like to relate an interesting historical anecdote related to the hidden benefits of fall protection. You can use it as a talking point with your workforce and it’s a good topic to discuss with the stakeholders who hold the purse strings to your safety equipment budget.
How leading edges are defined
A leading edge is any unprotected edge of a platform, floor, or other construction point where the elevation between the next level or the ground is greater than six feet.
Here’s how OSHA defines it. In its official publication, Fall Protection in Construction (OSHA 3146-05R 2015), OSHA states
The edge of a floor, roof, or formwork for a floor or other walking or working surface (such as the deck) which changes location as additional floor, roof, decking, or formwork sections are placed, formed, or constructed. A leading edge is considered to be an “unprotected side and edge” during periods when it is not actively and continuously under construction.
An example is when installing metal decking for flooring in a multi-story building.
A guardrail system would be an ideal solution for leading edge applications. But it’s not always feasible. Some form of personal fall arrest system must also be used.
So, let’s put this in real life terms. For work above 6 feet, construction workers and others know that fall protection is necessary. And most of the time, a worker can tie off to an anchor point above the D-ring on the harness.
However, leading edge work is different in several ways. First, there’s the edge itself. Often, it’s at the open side or edge of a building where the workers are laying decking, or performing other flooring or roofing tasks. In many cases, that edge is sharp, with either a very small radius or a 90 degree sharp angle. Should a crew member fall, the lifeline will come in contact with that edge. It’s often the sharp edge that could cut or fray the cable or webbing, particularly on impact. But, it’s also likely that the worker might sway back and forth while dangling over the edge.
Unless the worker falls directly in line with the anchor point, this pendulum style movement will naturally occur. That back and forth movement can quickly sever a lifeline cable or webbing that’s not designed for it.
The other potential hazard is the anchor point itself. The anchorage is usually below D-ring level, often at foot level. Low anchorage is necessary because there’s not always an overhead, approved attachment point, such as a wall or ceiling joist, and the lower anchor point doesn’t interfere with a worker’s arm movement. However, this means that the worker could fall farther before the deceleration device on the SRL or PFL catches. The lifeline might not reach the necessary speed to engage quickly enough to prevent some dangerous fall distances.
Not all PFLs or SRLS are designed for the low anchor points necessary in leading edge tasks. When combined, the leading/sharp edge and lower anchor point require specially designed fall protection equipment.
A basic personal fall arrest system consists of an anchorage point, connectors, and a body harness. (By the way, don’t even consider a body belt. They’ve been banned for fall arrest since January 1, 1998.)
Complete systems include a lanyard, deceleration device, and a lifeline. Some use PFLs (personal fall limiters), while other employ SRLS (self-retraction lifelines).
PFLs are limited to eight feet or less in length. SRLs allow for far greater range of movement, reaching as up to 20 feet or more. SRLs or PFLs may provide a safety option for leading edge operations. The anchor point in leading edge applications sits below the D-ring attachment on the harness, often at foot level. But, it’s the leading edge/sharp edge hazards that ultimately affect the design of leading edge fall protection equipment.
How leading edges affect fall protection design
ANSI (the American National Standards Institute) has even tougher standards and pays particular attention to lifeline performance in leading edge/sharp edge applications.
As mentioned above, a sharp edge is any non-rounded edge that can potentially cut, fray, or completely sever a lifeline or lanyard. The ANSI standard for testing the fall arrest device’s lanyard is dropping it over a steel bar with a radius of .005 inches or less. If there’s any severe damage or a complete separation at the point of impact, the device fails and it’s deemed noncompliant for a leading edge application.
The SRL must meet the conditions for dynamic performance, dynamic strength, and static strength as outlined in ANSI Z359. But, it must also pass the sharp edge test standard for leading edge approval.
By the way, only SRLs that pass the sharp edge requirements are permitted to include the LE designation on their label. So, be sure that it’s labeled “SRL LE.”
What to look for in leading edge permitted SRLs
The device must carry the SRL LE designation for use in leading edge/sharp edge work. But here are some other options to consider.
According to OSHA standards, every SRL (whether for leading edge or not) must be inspected prior to each use. Some devices come with a clear outer casing that let you visually check the cable, retraction dampening controls, and other internal components.
Any fall limiting device that is subjected to an incident must be taken out of service immediately, but you can put the device back into service quickly if internal components, cabling, and user-side shock absorber can be replaced onsite. This is a time saver if available.
By design, most SRLs are flat, disc-shaped mechanisms. Look for devices that include an integrated roll cage. This increases the life of the SRL LE by lessening damage caused by scraping along hard surfaces.
One final note:
Non-leading edge designated PFLS and SRLS cannot be used for leading edge or sharp edge work. But the reverse is not necessarily true. Fall arrest devices rated SRL LE can often be used in other applications.
You can save money by purchasing an SRL LE certified for other tasks as well.
Now… here’s that historical anecdote I mentioned.
The hidden benefit of effective fall protection
The year was 1933. The high-steel project? None other than the 1.2-mile-long Golden Gate Bridge, set to span the Golden Gate Straight where the San Francisco Bay emptied into the Pacific Ocean.
The problem? In those days, the number of fatalities expected was one man for every $1M of construction cost. The bridge was expected to cost well over $36M. For the lead engineer, Joseph Baermann Strauss, this loss of life was unacceptable. Along with other safety innovations—hard hats, wind goggles, and respirators, to name a few—he installed a unique, lifesaving form of fall protection.
A safety net was strung from one end of the bridge to the other. It was installed as each span was added. Once the net was in place, workers worked more quickly and efficiently, the fear of drowning all but eliminated. Nineteen men fell into the net, but they were saved from drowning in the ice waters of the Bay.
The result? The bridge was constructed $1.3M below budget… and months ahead of schedule. Fall protection can save lives, and that’s vital. But it can save time and money as well.
In a very real way, money spent on fall protection gear is not just a purchase… it’s an investment for—and in—everyone involved.