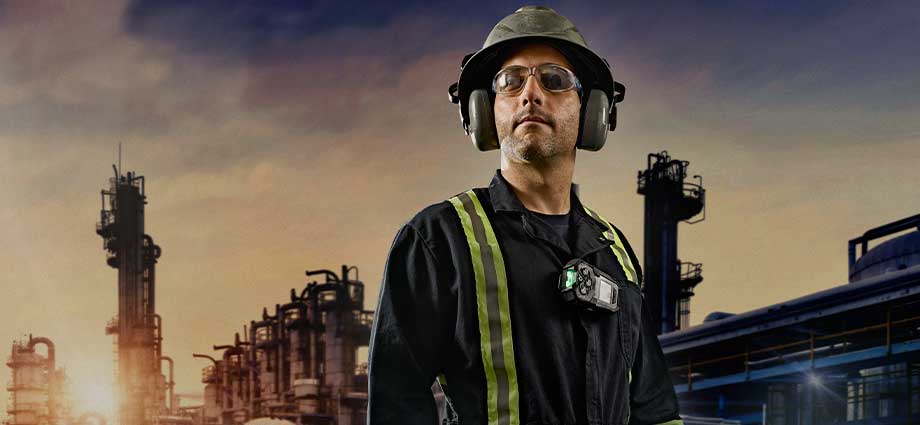
Turnarounds are regular, planned breaks in production at a petrochemical plant or oil and gas refinery to repair, inspect, test, or upgrade equipment. They require additional staff, and every minute the plant or refinery is non-operational costs the company money, which can make turnarounds expensive. Anyone who has experienced a turnaround at a plant or refinery knows the impact they can have on operations, employees, and safety.
Due to the monetary cost, high pressure, temporary workers, and additional safety risks, many companies take additional precautions during turnarounds at plants and refineries. This article will discuss some safety risks, focus areas, and available PPE to help keep workers safe while conducting this maintenance, so you can get your facility back up and running.
Some significant safety risks associated with turnarounds.
Turnarounds can last a few weeks, a few months, or in some cases, a major turnaround can last for a few years. The time required for a turnaround – and any issues resulting from inspections conducted during a turnaround – can impact revenue and overall project timelines; which often makes turnarounds fast-paced and high-pressure.
Here are a few significant turnaround risks:
-
New and temporary workers.
Turnarounds are big, complex jobs that often need to be completed in a tight window of time, and the workforce of a plant or refinery may balloon to accommodate the extra work. These new workers may not always start out being familiar with the hazards of the work area or the safety rules of the company.
-
Non-routine work.
Major turnarounds typically occur every few years, which means your workforce may be inexperienced or rusty regarding best safety practices and effective planning for specific non-routine work.
-
Longer working hours.
Due to the desire to get the plant or refinery back to regular operations as soon as possible, work shifts may be longer and more frequent for each worker.
Three focus areas that can help keep your workforce safe during your next turnaround.
-
Maintaining open communication.
Maintaining consistent communication with full-time workers and the large influx of temporary workers, including clear communication of safety standards and expectations, can help prevent workplace accidents. Pairing new workers with experienced workers, for example, is an excellent way to show them the ropes and help make the communication process more effective.
-
Training.
You already ensure that your existing full-time employees are trained and familiar with the hazards and best practices of your plant or refinery. Providing your temporary workers with the same level of care and consideration for the work they will be doing, such as site orientations, PPE and equipment training, and safety expectations, can also help prevent workplace accidents. For example, Certified Training Course options available either online or in-person to help prepare workers of all levels for a turnaround.
-
Personal Protective Equipment.
The nature of turnarounds means that workforces can grow by hundreds or maybe thousands of workers for jobs, including jobs that are not routinely performed, that may only last for a few weeks. As a result, many plants and facilities may not have enough supply of the proper PPE available to accommodate these workers. Consider planning ahead to have adequate supplies of the right PPE on site and ready to use at the start of your turnaround.
What PPE could you need during a turnaround?
Here are some important pieces of safety equipment to consider for your next turnaround.
Fall Protection
Turnarounds can present fall hazards for workers. Here are some options for selecting the proper fall protection for each unique application.
Latchways® Vertical Ladder Lifeline Kits provide hands-free movement on a fixed ladder and eliminate the need and risk of disconnecting and reconnecting during ladder ascent and descent.
V-SHOCK® SRLs help make SRL selection quick and easy, with distinct housing colors for leading edge vs. non-leading edge.
V-SERIES® Harnesses provide superior comfort and increased flexibility, with a racing-style buckle and pull-down adjustment that helps workers get the right fit that lasts throughout the shift.
Tool Tethers help prevent dropped objects, which can be especially helpful if the site has additional workers working at increased speed during a turnaround.
Head Protection
You may need additional head protection solutions for your workers.
Topgard Full Brim Hard Hats provide protection in high-temperature environments and wherever dielectric protection is needed.
V-Gard Cap Style Hard Hats provide top impact protection as Type 1 hard hats, while maintaining comfort and durability.
V-Gard H2™ Safety Helmets offer ANSI Z89.1 Type II certification to provide protection against top and lateral impacts caused by falling objects and equipment or slips, trips, and falls.
Gas Detection and Respiratory Protection
Opening up certain equipment in plants or refineries during turnarounds can release or create a risk of releasing explosive or toxic gasses. In addition to training, the right gas detection and respiratory protection can help protect your workers.
ALTAIR io™ 4 Gas Detection Wearable offers automatic cellular connectivity right out-of-the-box, to deliver real-time visibility to help drive safety and productivity.
G1 Industrial SCBA supports diverse respiratory protection needs, with a facepiece that allows for APR use with a variety of cartridge options and remote cylinder connection.
Visit msasafety.com to find the right PPE for your turnaround needs.