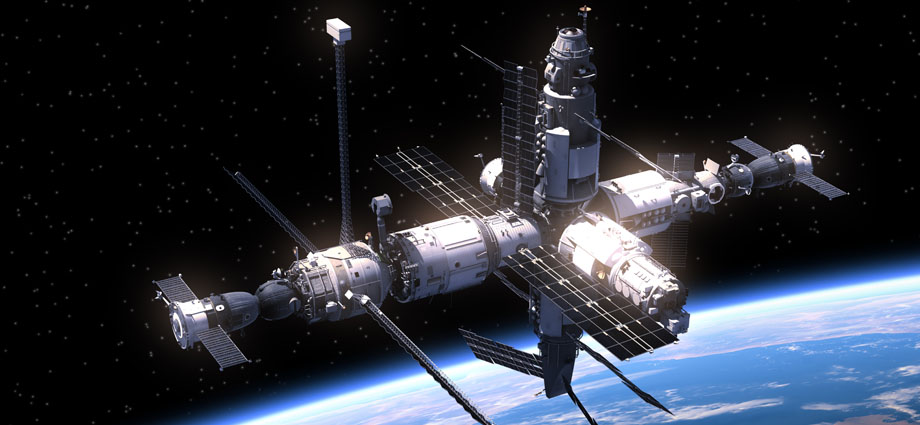
For MSA Safety, helping men and women stay safe does not apply to just those working on earth, but also to those working in space. Now onboard the International Space Station (ISS), MSA Safety’s combustible gas sensors are part of NASA’s Advanced Hydrogen Sensor Technology Demonstration.
Now onboard the International Space Station (ISS), MSA Safety’s combustible gas sensors are part of NASA’s Advanced Hydrogen Sensor Technology Demonstration. The system is testing new ways to keep astronauts safe by detecting hydrogen, a highly flammable gas.
MSA catalytic bead sensors are part of the Advanced Hydrogen Sensor Technology Demonstration that is testing an alternative technology to detect the presence of excess hydrogen in the output stream of the Oxygen Generation Assembly, which provides breathing oxygen to the ISS crew. Existing monitoring systems help to keep the ISS astronauts safe by alerting NASA to warning signs of high hydrogen levels onboard the space station. The test system reached the ISS in February with the system’s deployment expected to begin in April. The system is designed to demonstrate the suitability and reliability of the MSA sensors for use in space, after years of successful ground testing.
Brett Ashmore, MSA Safety Senior Field Sales Manager, has been a member of the MSA team involved in this sensor project that dates back a decade.
“Lives are at stake when providing breathing air to astronauts in space,” Ashmore said. “This is a great accomplishment to finally have our sensors launched, and we are really proud of our team. Seeing the sensors used in space is really a badge of honor for all of us.”
Known for their sensitivity, reliability, and longevity, MSA’s gas sensors have a history of performing in some of the toughest environments on the planet and are now going one step further. The sensors are manufactured by MSA in the United States and sold throughout the world.
“Our sensors are used in some of the most extreme operating conditions, like offshore oil and gas rigs, and it is exciting to see them proven to be effective in the aerospace industry,” Ashmore said. “In all testing, our sensors consistently performed with reliability, long life, and high accuracy, which we believe makes them a trusted choice for use on critical life support systems.”
MSA has a history of working with NASA dating back to the 1950s and 1960s. A part of the company, then called General Monitors, developed a hydrogen-specific catalytic bead sensor for Project Gemini to protect NASA workers and astronauts from explosions and fires. MSA played a role in Project Mercury with its canisters designed to absorb the carbon dioxide exhaled by astronauts and was involved in the Apollo Program by designing respiratory protection for NASA astronauts.
“We’re extremely proud of the work our associates have done in collaboration with so many organizations on this project,” said Greg Martin, MSA Safety Vice President of Strategy and Product Development. “This is yet another example of MSA’s innovation and reliability in the fixed gas and flame detection market and has led to additional opportunities for the company in the aerospace market. We are excited to be helping to keep people safe around the world and in orbit.”
For more information about the mission, please visit NASA’s mission page here.
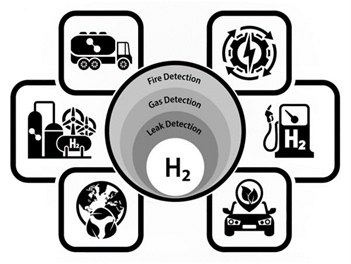
Work Safely with Hydrogen
Explore Solutions