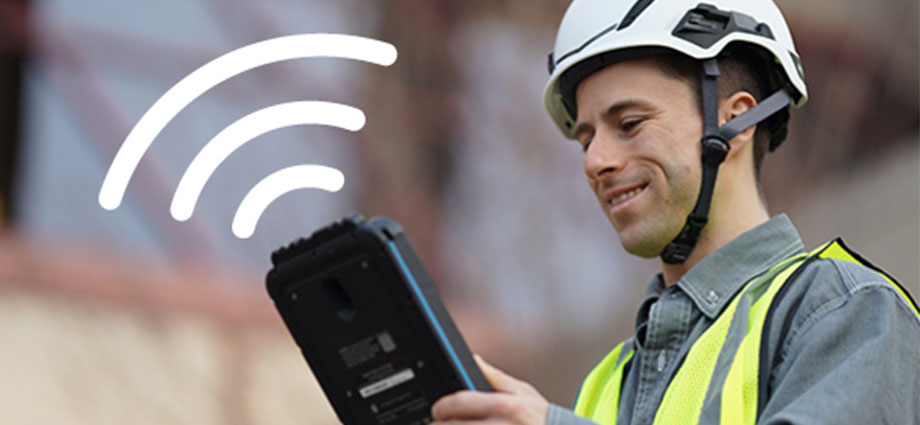
Cloud-based services aren’t new to the gas and oil industry; however, having access to a vast amount of data points gathered by sensors and devices can make it challenging to gather insights and develop an actionable plan. But with the right cloud-based service that offers simple features and an easy-to-understand interface, taking your data to the next level can be much more manageable.
With a centralized dashboard that can be accessed from anywhere with an internet connection, safety managers can leverage data for a proactive approach and informed decision-making while optimizing gas detector uptime.
Here are a few ways that MSA Grid clousd-based software can help to seamlessly turn your gas detection program into a comprehensive safety solution.
Help Improve Accountability Services
You and your team already use smart and connected devices in your day-to-day activities, from simple weather updates to online equipment manuals. Connectivity in all fields is becoming more and more common – and it should be no different when it comes to worker health and safety. Within this space, gas detection connectivity is meaningful while also a very straightforward field to leverage connectivity.
Cloud-based services for gas detectors can help safety teams in many ways, including improving response times while ensuring compliance with corporate safety policies and government regulations. Furthermore, safety managers turn to cloud-based accountability services to:
- Make improvements to the safety process.
- Discover new training opportunities.
- Stay aware of real-time notifications.
- Oversee plant safety remotely.
- Plan for maintenance for minimal downtime.
When you put compliance data in a centralized location, you save a considerable amount of time. For instance, the Alabama Power Company spent nearly 100 hours finding bump and calibration test data from gas detectors spread across multiple departments. However, after switching to the Grid Fleet Manager service, the corporation connected its devices to the cloud resulting in massive time savings.
Maximize Gas Detector Up-Time
When you have many portable gas detectors in the field, it’s tough to stay on top of sensors, bump tests and calibrations. Safety managers spend quite a bit of time reviewing when calibration is due or examining alarm events.
Yet, empty cal gas cylinders could delay bump testing or calibration, leading to downtime. Regardless of why your organization is behind on maintenance, it poses a risk to your workplace and employees.
Using MSA Grid software helps you develop a maintenance strategy complete with asset management, record keeping and preventative maintenance reports. A web-based dashboard lets you oversee equipment and identify potential issues before you experience downtime.
Moreover, having access to data presented in an easy-to-understand format helps safety managers see the big picture of a portable gas detector, including the sensor’s life-cycle. This critical information supports informed decision-making about replacement or repair timelines.
For Noel K. Campbell II, a Business Service Specialist at City of Asheville Water, Grid software assures them that “our detectors are ready for work, and we can verify that workers are using them properly – all in a fraction of the time we used to spend!”
Help Drive Safer Behavior
The only way to ensure working gas detectors is with regular bump testing, calibration and proactive maintenance. However, many workers can get complacent and don’t always catch sensor failure until it’s too late.
With cloud-based solutions, safety managers have access to real-time analytics and employee status information. You can be aware if detectors are ready for use and being used properly. Based on the data, you can take action or deliver timely feedback, which is crucial to worker accountability and early identification of the need of retraining them.
Use Accountability Services to Drive Effective and Efficient Processes
A cloud-based solution provides total visibility into worksite safety from building better training programs to increasing worker accountability. With MSA Grid and ALTAIR™ detectors, you get a connected system with an easy-to-use user interface, so safety managers can quickly create workflows for repairs and maintenance that make the best use of everyone’s time.
Learn more about how to help improve safety and accountability with a connected gas detection program.
