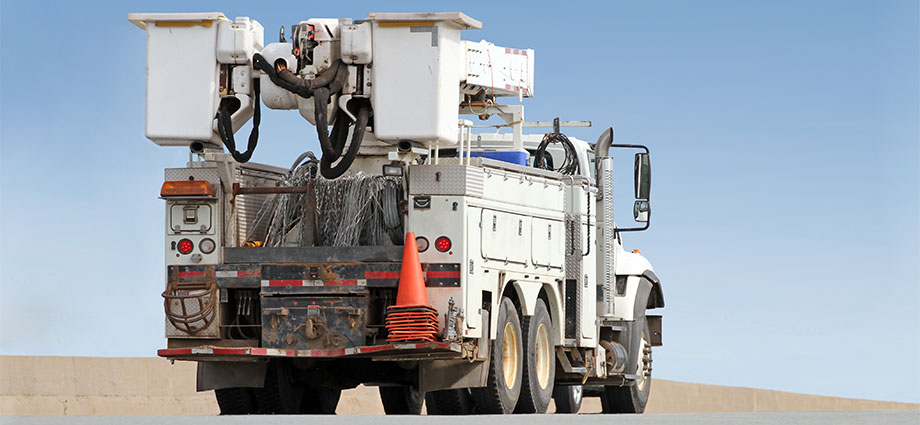
Hurricanes, tornadoes, torrential rains, and wildfires have been all too frequent topics in the news across the nation in recent years.
While it’s impossible to control the weather or natural disasters, it is possible to plan for the aftermath and response.
For the electric power industry, part of that plan is a well-designed emergency response and restoration process.
Partnerships Are Key to Restoring Power
So much of our daily lives depends on electricity to function. We rely on electric companies to provide a reliable supply of on-demand power, and the electric power industry has a strong track record of maintaining high levels of reliability.
But when natural and man-made disasters strike and cause significant damage to the energy grid, they can create widespread power outages.
Fortunately, electric companies plan constantly for these emergencies. Contingency plans are formulated, tested, and implemented. While many outages can be handled by the local electric company, large-scale disasters require a larger force of skilled industry workers.
To expedite faster, more effective responses, the Edison Electric Institute’s (EEI’s) member companies developed a voluntary mutual assistance program. EEI’s member companies, the nation’s investor-owned electric companies, work together to restore power safely and efficiently for customers.
For example, once it was safe and conditions allowed after 2018’s Hurricane Florence broke records for rainfall and caused widespread flooding, more than 40,000 workers from across the United States and Canada worked 24/7 to restore power. Impacted electric companies reported that they had restored power to more than 1.9 million customers, or approximately 97 percent, one week after Florence hit.
While cleanup from Florence was still underway, Hurricane Michael made landfall along the Gulf Coast as one of the four most powerful storms ever to impact the United States, causing widespread devastation, severe property damage, and immense human suffering across six states. Although Michael developed quickly—just 73 hours elapsed between the time Michael was first named as a tropical storm and the time it made landfall as a category 5 hurricane—electric companies mobilized an army of more than 35,000 workers from at least 27 states and Canada to respond. Never before have so many workers been mobilized so quickly.
Less than a week after Hurricane Michael devastated the Southeast, electricity was restored to more than 2.6 million—or 95 percent of—customers impacted by this catastrophic storm.
Orchestrating Effective Disaster Recovery
Restoring power after a major disaster can’t be haphazard. There must be a well-defined process to power restoration. It starts with ensuring that power is no longer flowing through downed lines and assessing any damage done to power plants, the primary source of electricity production. Following this, personnel inspect and repair the high-voltage transmission lines that serve thousands of customers over wide areas.
The next steps are to bring substations online for power to reach local distribution lines, followed by restoring power to essential services and facilities critical to public health and safety such as hospitals, nursing homes, fire and police departments, and water systems. Then, crews are dispatched to repair lines that will return service to the largest number of customers in the least amount of time. Service lines to neighborhoods, industries, and businesses are restored systematically. Once major repairs are completed, service lines to individual homes and smaller groups of customers are restored.
For major natural and man-made disasters, EEI’s mutual assistance program allows local electric companies to increase the size of their workforce by “borrowing” skilled restoration workers, along with specialized equipment, from companies in unaffected areas.
The mutual assistance groups are composed of partnerships formed through voluntary agreements between the electric companies within a region. Most agreements are managed by Regional Mutual Assistance Groups (RMAGs). There are seven RMAGs throughout the United States.
Electric companies and their employees make concerted efforts before disaster strikes to build an effective plan of action in preparation for large-scale outages.
This entails:
- Locating workers with specialized skillsets, including lineworkers, tree trimmers, damage assessors, and call center support personnel.
- Providing the necessary specialized safety training for these workers.
- Ensuring adequate safety gear is available to them, including hard hats, safety harnesses, and other necessary equipment.
- Locating additional resources that can be used for power restoration.
Getting the Lay of the Land
Before attempting restoration—and continuously during the event—workers need to be informed of conditions in the affected locations, their potential hazards, and the proper procedures for power restoration.
For example, de-energizing downed power lines is a priority for protecting restoration personnel, emergency responders, and the public from injury.
Command centers are set up in areas close to, yet protected from, affected areas. Planning possible locations and securing personnel in advance to staff these command centers ensures a smoother deployment when a catastrophe strikes.
When electric companies render mutual assistance to another company, there are other important considerations, including the physical and geographical conditions in the affected region.
If the location you’re going to has a different climate, you need to take that into account. This could affect the gear and clothing you bring.
For example, if you’re in the South and rendering assistance in a northern state, the often-colder weather may determine what garments you need to pack with you. Consider whether warmer shirts and pants, or even thermal underwear, are necessary to keep you comfortable and healthy.
Personal protective equipment (PPE) also may need to be considered. A colder climate may require that protective hard hat liners must be included in your gear. Stocking caps or full-face pullover caps might be necessary.
Of course, the weather may not be all you need to contend with. Insects and other wildlife vary with location. If you’re assisting in an area that has had standing water for a while, the mosquito population might be on the rise. Make sure your supplies include bug repellents and insect bite first aid supplies to ensure you can take care of any incidents.
And, finally, consider the terrain in the area. If the location is hilly or mountainous, particularly in rural areas, will you need to take along any special gear to navigate the topography?
Remember: these conditions can change with the seasons. Calling ahead before heading out is essential for determining your PPE equipment and other supply requirements.
Mutual Assistance Programs: The Keys for Major Disaster Recovery
Because of its unique structure, a mutual assistance program with RMAGs does more than just restore power to customers quickly and efficiently.
A well-planned program:
- Promotes the safety of employees, contractors, and customers.
- Strengthens working relationships across the electric power industry.
- Provides all EEI members access to skilled, qualified employees and contractors, regardless of size.
- Affords an effective process for sharing industry resources when disaster strikes.
If you and your team members are part of an emergency response team, make sure you’ve taken the proper steps to get the safety training necessary and secure the PPE you’ll need to manage your safety while on the road.
References:
http://www.eei.org/issuesandpolicy/electricreliability/mutualassistance/Pages/default.aspx