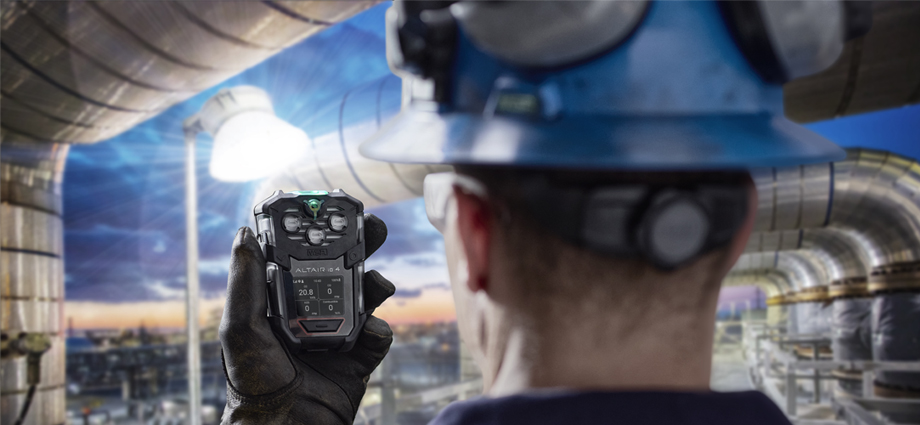
In the high-stakes world of oil and gas drilling, undetected gas leaks are one of the most significant risks that can put workers’ safety in jeopardy or cause potential delays or stoppages in operations. A single gas leak has the potential to ignite explosions or silently poison workers, with human safety and productivity consequences.
But what if you could detect these types of risks before they happen? Connected gas detection solutions play an important role in oil and gas drilling, helping to reduce risk, minimize downtime, and protect the workforce.
Gas Detection for Oil and Gas: Worker Safety
Oil and gas drilling operations are inherently risky due to exposure to dangerous gases such as methane, hydrogen sulfide (H2S), and other combustible or toxic gases. These gases can present a significant threat by increasing the risk of explosions, fires, and severe health problems for workers.
Hydrogen sulfide is considered to be extremely flammable and highly toxic, and according to OSHA, is one of the leading causes of workplace gas inhalation deaths in the United Sates.1 Many effects are seen even at low concentrations, ranging from mild, including headaches or eye irritation, to very serious, such as unconsciousness and even death.1 Hydrogen sulfide is detectable by smell at low concentrations, but at toxic levels, it causes what is known as olfactory fatigue, making it almost impossible to detect by scent alone.2
Exposure to hydrogen sulfide can come from various sources, such as crude oil processing or equipment like scrubbers, which are designed to capture emissions. Detecting gases in drilling operations presents several unique challenges. Environmental conditions are often harsh, with extreme weather, high winds, and fluctuating temperatures, which can make it difficult for traditional detection systems to work reliably.
Gas Detection for Oil and Gas: False Alarms and Predictability
False alarms are often another common concern. If detection systems aren’t accurate, unnecessary shutdowns may occur, resulting in costly halts in production. Studies show that just 3.65 days of unplanned downtime per year can lead to losses exceeding $5 million for an oil and gas company.3 Reducing the frequency of false alarms can help maintain operational efficiency while keeping workers safe.
Gas leaks in drilling operations can also be unpredictable. Leaks can occur around equipment or in confined spaces, where gas accumulation is rapid and often undetectable – and which often require more complex entry and exit protocols and additional PPE and safety measures.
The Role of Connected Gas Detection in Safety and Productivity
Wearable, connected gas detection solutions can help mitigate incidents that may put workers at risk or result in unnecessary downtime. Connected gas detection solutions, such as the MSA ALTAIR io™ 4 Gas Detection Wearable, which comes with automatic integration with Grid cloud-based software, provides continuous monitoring of hazardous gas levels, alerts workers when dangerous conditions arise, and enables off-site safety managers to know when and where there’s a call for help. This type of connected safety approach can help organizations address gas leaks quickly and issue evacuation alerts to targeted crews when needed.
Grid Shared Alerts, available with ALTAIR io 4 devices, notify those on-site directly on their devices if a nearby worker or another worker in their group has gone into alarm. This allows workers to act quickly to evacuate, respond to a worker emergency, or contact first responders.
High-quality sensors can more accurately detect gas leaks, helping ensure that operations are only interrupted when a genuine threat is present. By accurately detecting leaks and differentiating between false positives and real threats, a connected solution with real-time monitoring can help prevent unnecessary interruptions, allowing workers to remain productive and operations to continue smoothly.
The Grid Insights Alarms Dashboard, available as part of Grid software, provides safety managers with a historical overview of where and when alarms are triggered, tracking both genuine incidents and false alarms across multiple jobsites. This insight helps managers identify trends in device performance and operational areas prone to more frequent alarms. Over time, this data allows organizations to proactively adjust their safety protocols, helping to improve both worker safety and productivity while minimizing disruptions.
Key Benefits of ALTAIR io 4 Devices for Onshore Drilling:
- Cellular Connectivity: Helps enable worker visibility with live monitoring capabilities, while fleet compliance is streamlined with over-the-air updates and automated bump tests and calibration.
- Device Durability: Built to withstand harsh conditions, the ALTAIR io 4 detector can survive drops of up to 25 feet and has an IP68 rating, making it dustproof and waterproof.
- Sensor Lifespan: MSA XCell® Sensors lead the industry in durability, with a typical lifespan of up to seven years, helping to reduce the need for frequent replacements and maintenance.
See the ALTAIR io 4 in action in this brief video demo.
1. https://www.osha.gov/hydrogen-sulfide
2. https://www.osha.gov/sites/default/files/publications/OSHA4204.pdf