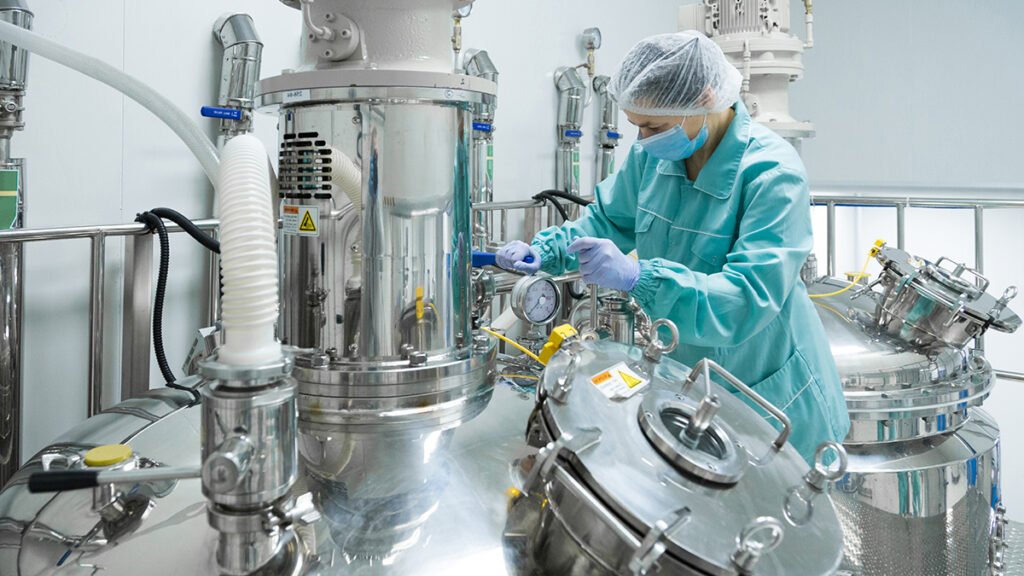
Typically, when we think of inserting / tank blanketing a process vessel, we think of a tank containing some type of flammable substance with a vapor layer on top. The tank is then filled with an inert gas whereby reducing the risk of combustion. However, there are many instances when there are no flammable liquids or vapors, but simply a very fine combustible dust. Anybody who has created a small fire burst using non-dairy creamer and a lighter can relate to the potential for a fire in a larger scale. Other examples of the potential devastating effect of dust in fires of explosions are grain storage silos which on occasion will be shown on the nightly news. In this article we will explore how inserting can work to help preventing fires in vessels containing combustible dusts.
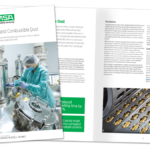
Download your copy of this success story and find out how MSA Safety’s gas inerting experts can help you to remotely qualify your system and provide cost savings for reduced travel and expenses.
Download the PDFA large pharmaceutical manufacturer in the Northeast area of the US had 12 mixing hoppers used to combine components for a controlled type medication. The medication would then be packaged in capsules. The mixing hoppers were relatively small in size at about 25 gallons in volume, as they were designed to work in small batches, with a large number of them in the same working space. The batches were kept small to reduce risk in case a batch had to be rejected due to very exacting quality standards for the product.
Concern
The powder components were individually loaded into each hopper manually from bags. In order to accomplish this, the operators opened the top hatches to pour in the contents of the bag. Every time the hatches were opened, the vessel also filled up with air and caused a safety concern due to the presence of oxygen.
Each vessel was connected to a nitrogen line that would purge the headspace; however, the operators needed to know when the space was truly inerted so they could start the mixing process in safety. Nitrogen was supplied to the vessels on a time basis mode, with the time calculated to err well on the side of safety. If the inerting time could be shortened, the process could be expedited, and production increased.
Another concern was cost. The product was handled in small batches in different hoppers, but there were 20 of them operating at any single time to be able to keep up with production. Having a separate dedicated inerting system for each unit was not economically feasible. In addition, hoppers were filled sequentially, so not all of them had to be inerted at the same time.
Solution
The plant production group at the company determined that the most efficient, and safe way to handle inerting was to analyze the head space for oxygen and to stop nitrogen flow once the desired level was reached. This avoided the uncertainties of knowing exactly when each vessel was inerted. The fact that only one vessel had to be analyzed while it was actively being worked on, gave them the idea of using a portable type system that could be moved from vessel to vessel as needed.
MSA Gas Analysis engineers suggested and developed a full inerting control system mounted on a stainless-steel cart with wheels. The cart was equipped with a flexible hose that could be connected to a particular tank to draw a sample and determine if nitrogen still needed to be added into the vessel. It also had the sample conditioning package, oxygen sensor and analyzer on it. In addition, the cart was fitted with a set of warning lights that would alert the operator of the condition of the vessel: red indicating the inerting process was not complete and green indicating that the nitrogen intake could be shut off and the mixing process could start. Alarms were also added to provide additional warning/information to the operators.
Once the system was operational, operators would open the valve to the line feeding nitrogen into a vessel, fill it with the desired products from bags, close the hatch and connect the mobile analyzer to the hopper. When the analyzer indicated an inert status within the vessel, they would shut the nitrogen off, disconnect the analyzer and start the mixing process.
It is important to emphasize that the open hatch period during which the hopper is being filled is one of the most critical times from a combustion-safety perspective. Maintaining the proper flow of nitrogen during this time is critical since air is freely flowing in through the open hatch.
The plant team reported that the payback period for the system, considering the improvement in productivity was quick and measured in months, with the added benefits of enhanced combustion risk reduction. Improved revenue from production and a safer combustion-related process is a great combination.
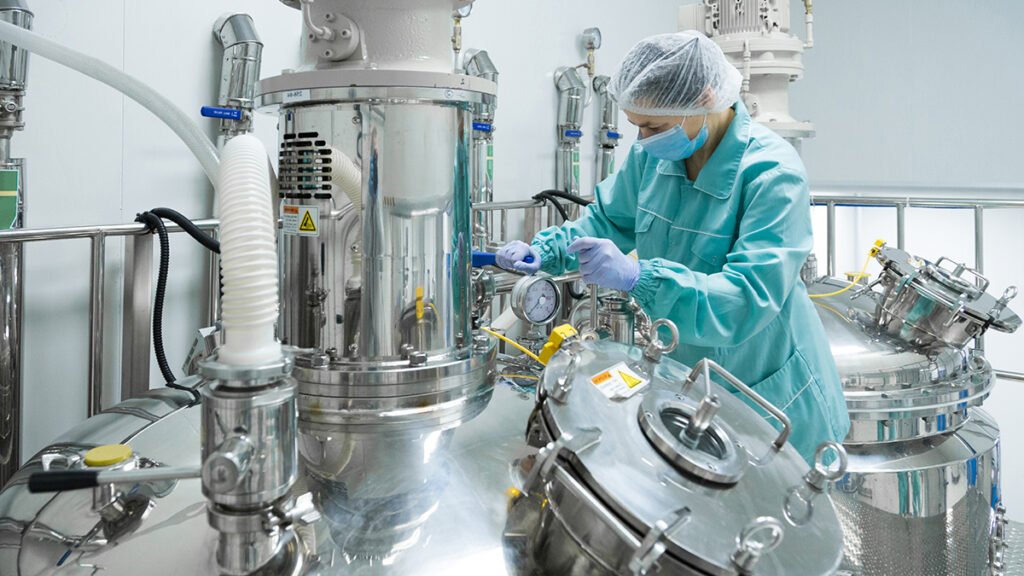
Conclusion
The use of an analyzer-based oxygen inerting system proved to be a win-win for the customer. It allowed them to, first and foremost, ensure that combustion risk was always contained by keeping oxygen levels below the necessary threshold to avoid the chance of combustion. In addition, the customer achieved the additional improvement in its production rates with a quick payback on the investment in equipment.
The mobile analyzer cart that was designed for this customer by our application engineers, shows the ingenuity, capability and level of customization that MSA can offer to achieve a customer centric solution.
MSA industrial process analysis experts are available to help in a variety of applications. For assistance, provide project details at myBacharach.com/GAsurvey and one of our application engineers will discuss ways to optimize your process.