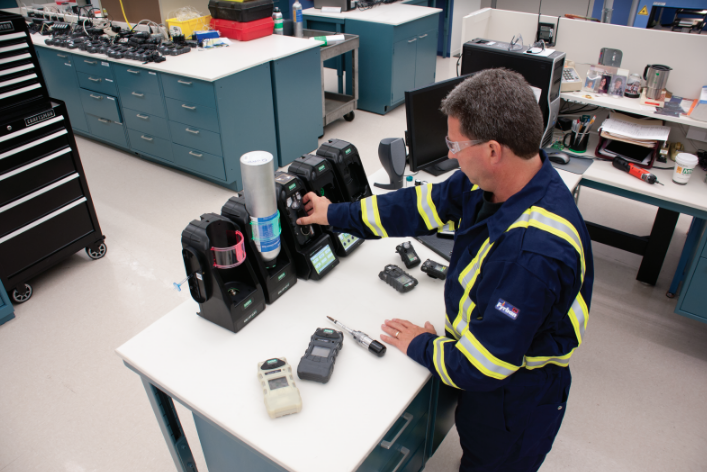
If you work with direct-reading portable gas monitors (DRPGMs) to check oxygen levels and look for toxic or combustible gases, you’re likely familiar with the concepts of bump testing and calibration. But if you were given an on-the-spot pop quiz on the subject, could you tell the difference between these terms?
The main difference between a bump test and calibration is that a bump test determines whether a DRPGM can detect if a possibly hazardous gas is present, while calibration checks that equipment is accurate.
But it’s a little more complicated than that, and getting to know more about bump tests, the two types of calibration, and related best practices can help you keep these distinctions top of mind—and use them correctly.
Defining Differences
Direct-reading portable gas monitors fall under the responsibilities of safety equipment trade organization the International Safety Equipment Association (ISEA), which released a 2010 statement to improve consistency in how people use, test, and maintain DRPGMs. In that statement, the organization was careful to flesh out the differences between a bump test, calibration check, and full calibration as well as advise how and when to test with each method.
So What’s a Bump Test?
The ISEA defines a bump test as a
“qualitative function check where a challenge gas is passed over the sensor(s) at a concentration and exposure time sufficient to activate all alarm indicators to present at least their lower alarm setting. […] This is typically dependent on the response time of the sensor(s) or a minimum level of response achieved, such as 80% of gas concentration applied.”
This checks whether sensors and alarms are working as intended, and failure might indicate that a blockage is present. In sum, bump testing assesses function, not accuracy.
How Is Calibration Different?
Part of the confusion surrounding bump testing versus calibration lies in the fact that calibration checks and full calibration are two different things. Both of these types of calibration can test a DRPGM’s accuracy, but they’re used in different circumstances.
A calibration check, according to the ISEA, is a
“quantitative test utilizing a known traceable concentration of test gas to demonstrate that the sensor(s) and alarms respond to the gas within manufacturer’s acceptable limits.”
Calibration checks start by “zeroing” a DRPGM (resetting it to a reference point determined by the manufacturer) and testing that alarms go off after applying a high enough concentration of test gas. The resulting sensor reading should match the concentration listed on the test gas container. The ISEA says that a device is accurate within an acceptable range that’s “typically ±10-20% of the test gas concentration applied unless otherwise specified by the manufacturer, internal company policy, or a regulatory agency.”
The ISEA guideline describes full calibration as
“[t]he adjustment of the sensor(s) response to match the desired value compared to a known traceable concentration of test gas.”
This adjustment accounts for naturally occurring drifting and other environmental factors. Specially trained, qualified personnel are the only people permitted to perform full calibrations.
Bump Up Your Bump Test Knowledge and Avoid Calibration Frustration
Now that you know the differences in definition, let’s take a look at some tips and tricks for using both bump tests and calibration.
When to Test
Perform a bump test and calibration check every single day before anyone uses the DRPGM that day (and according to manufacturer’s instructions).
The DRPGM’s manufacturer’s guidelines—plus internal policies and regulatory recommendations—determine exactly how and how often to fully calibrate that particular DRPGM. Full calibration is also necessary if a bump test or calibration check fails. You can perform a full calibration twice, but after two “fails,” the device must be pulled from use. Full calibrations should also take place after the following types of exposures:
- Different operator or working environment
- Extreme environmental, storage, and operating conditions
- Highly concentrated target gases and vapors
- Solvent vapors and corrosive gases
- Poisons and inhibitors
Testing Best Practices
When testing a device, use the following guidelines:
- Perform the calibration in fresh air
- Choose a test environment with conditions that match your workplace
- Use a recommended gas mixture, which should meet the National Institute of Standards and Technology (NIST)
- Check the gas’s expiration date
- Always refer to your product manual for specifics
Keep a Record
It’s essential that you keep records of all device testing and maintenance. Should a user experience a reportable event with one of your devices, the Occupational Safety and Health Administration (OSHA) needs to see a history of all bumps and calibrations during the year prior to the incident. But even without an incident, testing and maintenance data can track other valuable information, and new technology makes record-keeping easier and more valuable than ever.
Digital tracking and remote monitoring are just some newer technologies that automatically track and allow you to manage your fleet’s bump tests and calibrations from wherever you are. Some can even be paired with GPS devices so that you always know where your workers are. If you detect that they’ve been exposed or if a man-down alarm indicates that a worker experienced a health emergency, you know exactly where to send help—and what kind of help to send.
Interested in simplifying the management of your gas detection fleet with automated calibration? Learn more about the MSA GALAXY® GX2 Automated Test System here.