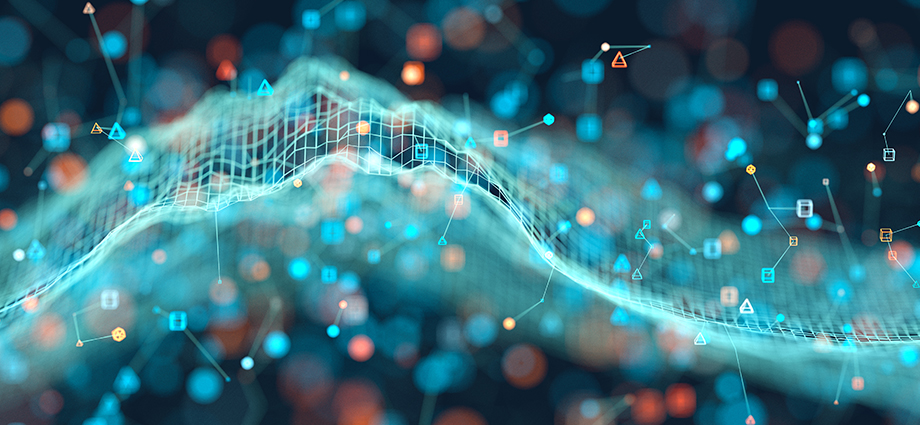
Access to data is essential for maintaining gas detection safety programs. And there’s a good chance that you already have plenty of details about incidents in your workplace. But are you using this information to your advantage? And what is the amount of effort that you have to make to draw insights from that data?
As safety management evolves to include proactive and preventive measures, the impact of data is clear. It does more than keep your company compliant. Data can help provide clarity on the most simple questions, such as how many gas detectors you have in your fleet vs. how many you actually use. But it can also contribute crucial information on much more complicated topics by providing in-depth insights.
When looking into your gas detection safety program, how easily can you answer the following questions?
- How many portable gas detectors do you have in your fleet?
- How many of those detectors are available and ready for the job at any moment?
- How many units are currently in use?
- How many times were the devices on? And can you get a report?
In addition to helping you stay compliant and manage your fleet more efficiently, there is so much more your data can do for your teams, company, and gas safety program.
Data about exposures can:
- Inform risk assessment and make reports more realistic and reliable.
- Provide the knowledge needed to manage, treat, and mitigate specific risks.
- Identify unsafe conditions and help to build a safety culture.
Safety managers can use data to form comprehensive evaluations that help to drive safety goals and actions.
The Impact of Data on Loss Prevention
Although loss prevention activities are key to making industrial processes safe, few actions or methods are mistake-free. Since roughly “80% of industrial accidents are caused wholly or partly by human actions,” using data to assess worker responses to alarms can help leaders proactively address threats.
Moreover, equipment design and connectivity allow data gathering and analysis that can be used to improve procedures and support training to reduce the likelihood of human errors. Yet, for these to be effective, leaders must be able to use the data at hand to inform and continuously adjust methods to help mitigate risks and prevent losses.
Understanding the role of data in your loss prevention and safety programs and leveraging it to influence outcomes can help improve workplace safety. Furthermore, placing data at the center of your operations gives safety managers countless opportunities to almost instantly provide feedback to workers and create a stronger safety culture.
The Impact of Data on Worker Accountability and Better Safety Behaviors
There are many reasons why workers fail to follow safety rules. In some cases, the risk is thought to be minimal. Employees may feel company efforts to instill proper safety behaviors are based solely on compliance, not on real-life situations and risks. Others may let their guard down as they become familiar with a process. All of these instances can lead to adverse outcomes impacting your safety and operational goals.
The use of data helps safety managers take meaningful actions and deliver feedback. Using services like MSA Grid cloud-based software, leaders can identify unsafe behavior associated with improper use of portable gas detectors and link that to individual workers or locations. Acting on this information, communicating with teams and re-training them allows safety managers to have a real impact on worksite safety.
Plus, your safety data provides invaluable insights into near-misses and incidents. Leaders can use these details to boost awareness and help workers avoid future incidents.
The Impact of Data on Automating Actions
The administrative side of gas safety programs is time-consuming. It requires a great deal of proper recordkeeping and continual checks to ensure compliance. Each time employees stop to check portable gas detectors for maintenance and compliance, it halts their work and disrupts their focus.
Compliance automation is critical both to productivity and workplace safety:
- It allows safety managers to be more efficient and effective with compliance related tasks, including equipment maintenance and incident reports.
- It optimizes operations uptime as it reduces the risk of non-functioning equipment.
- It makes control of equipment inventory easier and helps to avoid unnecessary purchases.
- It gives workers and supervisors peace of mind, as they are sure the equipment has their back.
Connected devices and services also send information that helps detect risks and inform decisions about gas safety program objectives.
Connected Safety Programs: A Model for Today
As the focus on prevention is fundamental, a proactive approach based on information is paramount to gas safety programs.
Moving forward, leaders can use data from connected devices to accurately assess risks, collaborate with teams, and learn from incidents. As organizations embrace a safety culture based on data, employees benefit from on-the-spot training and peace of mind.
Learn more about how the MSA Connected Work Platform can help you build a connected safety program.
Sources:
http://158.132.155.107/posh97/private/Dissertation_resources/Human_factors/Human_error
https://www.sciencedirect.com/science/article/pii/S0950423020306173