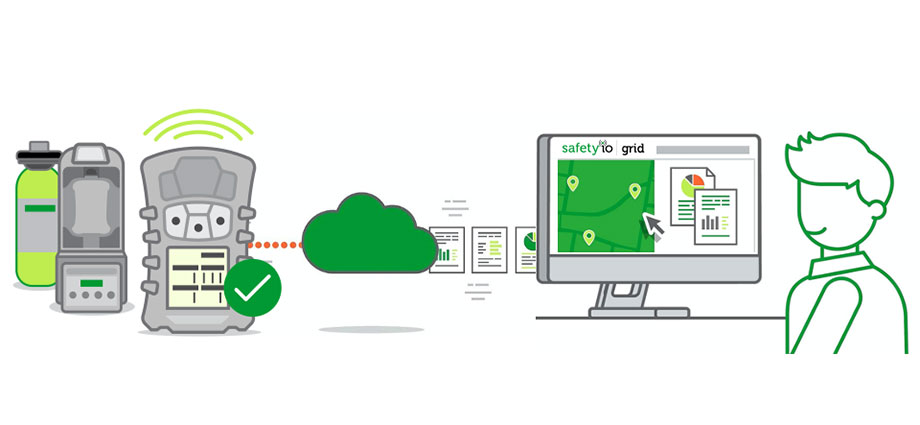
Many organizations take advantage of cloud-hosted infrastructure to stay connected with remote teams across the world. And these same cloud-based systems are transforming portable gas detectors and area monitoring.
By pushing data to the cloud, you can access collected information from anywhere with an internet connection. Plus, intuitive browser-based software makes it easy for managers to navigate situations and take action quickly. Here are 5 actionable ways cloud-based safety monitoring systems can help you improve your gas detection program
1. Monitor Workplace Safety from Anywhere
You may have dozens or hundreds of employees using portable gas detectors across many locations, making it difficult for on-site crews to monitor daily activities, and even more challenging for those off-site to review real-time data and insights.
However, with an online monitoring portal, your Texas team can easily review incoming reports from a plant in Canada. Cloud-based solutions provide increased visibility, even in the most challenging jobs such as confined space entries where the full visibility of gas readings and exposures is critical.
Safety managers can oversee early warning device data from any location with an internet connection. Whether it’s working from home or stepping out of the facility for a short period of time, managers are able to stay up-to-date with the latest occurrences.
Cloud-enabled devices and software send details of each detector, reading and crew member exposure to the cloud. You receive notifications or emails of important alerts. Or you can check the latest numbers on your dashboard, which presents information in a friendly format requiring no special training to understand.
2. Be Proactive
Traditional systems rely on employee and manager reporting, which may come with a lag time. Yet, time is of the essence in your industrial plants. Each second an alert goes unnoticed threatens worker safety and factory compliance.
A world-class gas detection program provides early warning to help you protect plants, personnel and assets. With real-time notifications, your teams can immediately take remedial or preventive actions to handle sensor checks or warning alerts.
Moreover, a cloud-based solution gives managers the facts to address worksite safety concerns before they turn into escalated issues. Don´t wait until you see a pattern of complacency. Instead, you can take action with a proactive approach to addressing safety concerns.
3. Develop Total Visibility Over Your Safety Program
As gas detection evolves, an integrated monitoring and safety system lets you get a handle on big data. Technology moves data safely from all portable gas detectors into a secure cloud environment. From there, you can drill down into the small data, the information that informs your daily decisions and affects productivity.
With data centralized and placed into a friendly display format, your managers and leaders get a 360-degree view of safety operations within your plant. Every action and daily activity taken at the plant can be tracked in order to deliver data and insights that you can use to solve informational gaps and help avoid safety incidents.
4. Drive Employee Accountability
Teams may get complacent or feel a false sense of security when it comes to portable gas detector alerts. Real-time situational awareness plays a huge role in safety at your plant. With a proactive approach to safety, worker wellbeing and productivity, you can support your workforce while improving safety and efficiency.
Cloud-based monitoring software drives worker accountability by making your expectations clear, giving you opportunities for instant feedback and helping you view data logs and response times by employee, department or location.
5. Make Data-Backed Decisions
61% of executives believe “their companies could rely on data analysis more and intuition less,” according to PwC. However, many leaders face an overwhelming amount of big data with no reliable way to break them into actionable insights.
With a cloud-based gas detection program, executives can quickly review data logs, measurements or response times. A convenient dashboard with easy-to-read reports supports data-driven decision-making.
You can spot patterns by examining historical data or calculate the timing for a partial or total shutdown for maintenance.“ With access to information, it’s easier to pinpoint which plants need a higher level of training or where you can adjust your approach to drive better worker accountability.
Oversee Operations With Cloud-Based Solutions for Your Gas Detection Program
As management teams continue to work remotely, the need for cloud-based solutions is essential. One solution to empower your safety managers and drive worker accountability by establishing a connected gas detection program. Learn more here.
Sources
https://www.pwc.com/us/en/services/consulting/analytics/big-decision-survey.html Accessed November 8, 2020.