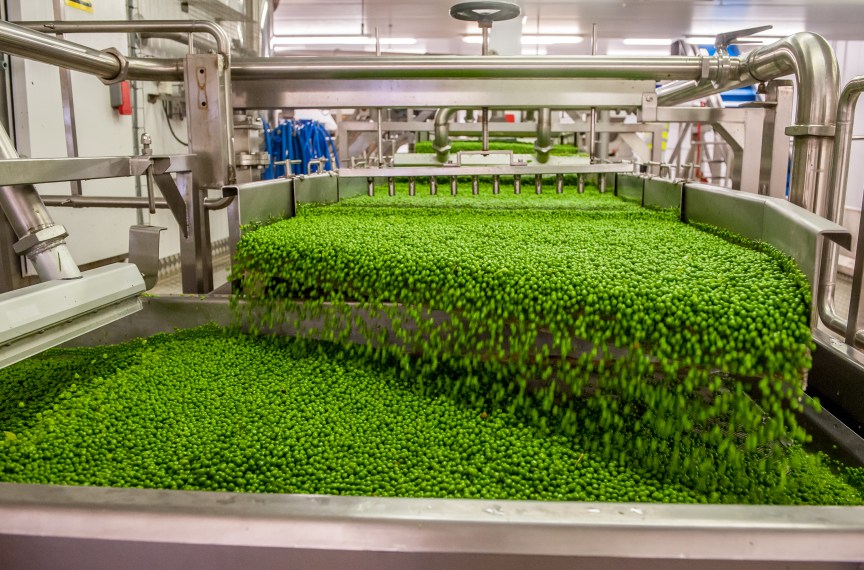
Download a copy of the Greenyards Frozen Ammonia Safety Compliance case study
Greenyard Frozen Improves Ammonia Safety Compliance
With 20 tons of hazardous ammonia on site and a packing capacity of 500 tons of quality frozen food per day, refrigerant leaks posed a costly problem not just in case of slowing production but also for safety compliance. Greenyard Frozen needed a robust refrigerant leak detection and notification system. Bacharach’s complete end to end solution was low maintenance and cost effective utilizing industry leading ammonia leak detection and trusted, reliable online notification software platform.
Greenyard Frozen has over 50 years of experience and is a worldwide leader in providing fresh-frozen, high quality fruits and vegetables.
The King’s Lynn production site in the UK is one of 10 sites across Europe. The British Retail Consortium (BRC) accredited facility boasts a freezing capacity of 28t per hour / 55,000 tons per annum with a packing capacity of 500t per day. With a total of 7 packing lines along with blast freezers and coldstore requirements, a total amount of 20 tons of ammonia on site is required. With an operation of this magnitude and a focus on maximizing freshness and product quality, a cost-effective, low maintenance refrigerant detection system was needed — keeping costly and damaging refrigerant leaks to a minimum.
Ammonia Safety Compliance
Julie Howlett, HR, Health, Safety & Environment Director for Greenyard Frozen UK explains, “Ammonia is extremely toxic at low levels and also has the potential to be explosive given the right conditions. With continuous improvements in the engineering rooms, we wanted to provide low level protection for personnel while also keeping high level protection for the Dangerous Substances and Explosive Atmospheres Regulations.”
Despite having zero global warming potential (GWP) and zero ozone depletion potential (ODP), Ammonia (NH3 / R-717) and being the most environmentally friendly refrigerants there is, it is also considered a high health hazard because it is corrosive to the skin, eyes, and lungs. Ammonia levels of 300ppm are considered immediately dangerous to life and health and it is flammable at concentrations of approximately 15% to 28% by volume in air. It was therefore a vital requirement for Greenyard Frozen’s King’s Lynn site to have a robust refrigerant management solution in place that incorporated reliable refrigerant leak detection equipment and a trusted refrigerant leak notification service. Julie Howlett continues, “Bacharach provided the complete turnkey package from the installation of the gas detection equipment through to their connected 24/7/365 online platform to spot trends and set up email alerts. It ticked all the boxes in what we were looking for in a detection system.”
Industry Leading Ammonia Leak Detection
The completed system employed five Bacharach Multi-Zone (MZ) Refrigerant Monitors, capable of industry leading refrigerant detection down to 1ppm.
In addition, each MZ unit was able to monitor up to 16 zones through the innovative aspirated system. Matthew Bilverstone, Greenyard Frozen’s Coldstore Refrigeration Engineer explains, “Traditionally we used fixed point sensors but with the ongoing costs and maintenance we looked at different systems. The aspirated system came on top. Maintenance costs are dramatically reduced and parts are easier to change thus reducing callouts.”
The aspirated ammonia system was around half the price of an equivalent point sensor solution for the refrigerant monitoring. Additionally, from a maintenance perspective, maintaining five aspirated monitors in comparison to approximately one hundred individual point sensors provided massive savings.
Bacharach’s MZ unit offers much more than just low maintenance costs and excellent low-level gas detection. The MZ unit is able to expand up to 48 monitoring zones using spur kit extensions, with the high performance pump providing detection distances up to 1,200ft (365m) from the main unit. The large graphic LCD display and LED status indicators provide a system-wide overview at a glance. However, what really sets the MZ unit apart is the ability to provide data-driven functionality when combined with the Parasense platform.
System Design, Installation and Implementation
With over 30 years of helping industries detect refrigerant leaks, the Bacharach team’s expertise was put to good use through the design and installation of the leak detection equipment and deployment of the refrigerant management software. Knowing where to place sensors when it comes to airflow, refrigerant density and area size are key considerations for early leak detection and, in this case, for safety compliance.
There was a tight time-frame to install the refrigerant leak detection system across the entire site that needed to fit in between crop delivery and harvesting. However, as Matthew Bilverstone explains, “The engineers that came to site were professional, efficient and took care and time in every aspect. They completed it within the required time frame with regular visits being made from the project leaders to ensure we were happy and worked closely to meet our requirements.”
The Parasense Refrigerant Management online software
Robust Data Driven Notifications
In addition to the industry leading hardware, Greenyard Frozen also deployed Bacharach’s Parasense Platform- the data driven refrigerant management software. The software provides full refrigerant monitoring across the whole site from a single point of reference. As Matthew Bilverstone continues, “It’s a brilliant piece of web-based software it can be looked at from any device anywhere. With ongoing trends you can look at past data, set limits and see what areas are causing the most problems then organize repairs once the leak has been found.”
Each sample taken from the hardware is timestamped and securely stored within the cloud database. This means that reports can be generated over whatever time-frame is required, allowing the ability to review refrigerant leaks across all the appliances, easily identifying problem equipment. What’s more, for compliance issues, there is a clear auditable trail of each leak event, the time and date of the event, how much ammonia was detected and how the leak was speedily repaired.
Conclusion
The complete Bacharach system has helped Greenyard Frozen continue to provide high quality frozen foods both safely and efficiently with a reliable, cost effective, low maintenance ammonia refrigeration leak detection system. The system provides greater visibility, understanding and a new, innovative way of managing leak events. As Matthew Bilverstone concludes, “We are now regularly checking for trends and preventing more serious leaks appearing. Our main project objective was to introduce a low-level detection (50ppm) to alert and protect personnel which has been achieved.”