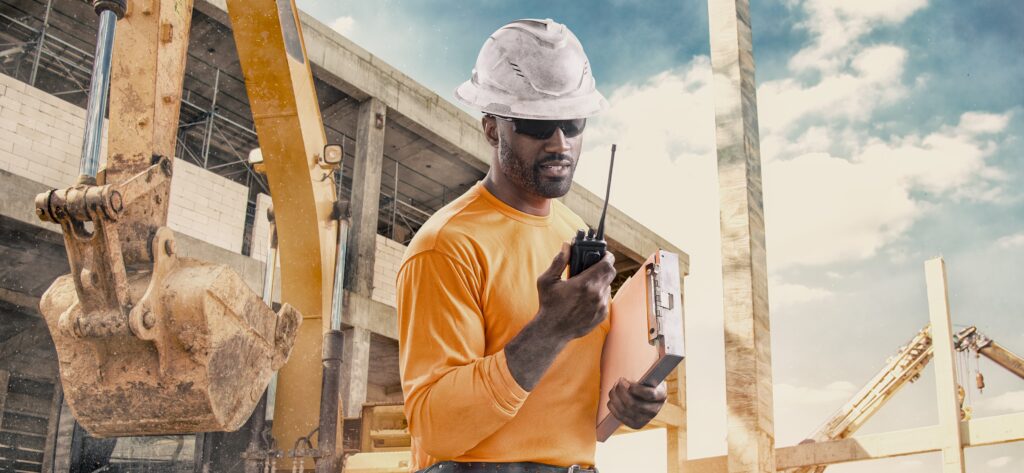
Seasonal heat stress can pose a significant risk to workers, particularly those working in construction and demolition operations. According to the Bureau of Labor Statistics (BLS), there have been nearly 34,000 work-related heat injuries and illnesses involving days away from work from 2011 – 2020; with an average of nearly 3,400 heat-related injuries and illnesses each year.1 Recognizing the critical need to address this hazard, the American Society of Safety Professionals (ASSP) published the first national voluntary consensus standard addressing workers in construction and demolition operations.2
Released in February 2024, the standard “offers guidance on protecting workers; explains how to acclimate workers to high heat conditions; and provides requirements for training employees and supervisors.”2
What is an ANSI/ASSP Voluntary Consensus Standard?
According to ASSP, “Voluntary consensus standards provide the latest expert guidance and fill gaps where federal standards don’t exist.” ASSP continues to explain that companies rely on them to drive improvement, injury prevention, and sustainability.2
The standard features checklists and flowcharts designed to help companies develop clear and effective heat stress management programs that bridge the regulatory gap.2
While this standard focuses on construction and demolition, ASSP notes that the “guidance can be adapted to protect workers performing other outdoor jobs such as tree trimming, farming, road maintenance and pipeline painting.”2
What are Common Seasonal Heat-Related Health Risks for Outdoor Workers?
The standard explains that a variety of personal risk factors can increase susceptibility to heat stress and notes that providing workers with the keys to recognize the warning signs of these common heat exposure illnesses and conditions can be included in a worker training program:3
- Heat Cramps: These types of cramps are associated with the body’s depleted salt and water levels from excessive sweating and often occur in the arms, legs, or abdomen.
- Heat Rash: Symptoms of this skin irritation are tiny bumps that may be painful or itchy and are surrounded by red skin.
- Heat Syncope: Short duration fainting or dizziness resulting from physical exertion or rapid postural change in high heat environments.
- Heat Exhaustion: A cardiovascular insufficiency due to demands of sweating caused by working under heat stress conditions and exacerbated by dehydration. Heat exhaustion may lead to Heat Stroke.
- Heat Stroke: Heat Stroke is the most serious heat-related illness and occurs when the body is unable to adequately dissipate heat, losing the ability to regulate core body temperature. Heat Stroke is considered life-threatening and requires that the victim receive medical attention as soon as possible. Signs include confusion, slurred speech, very high body temperature, seizures, and loss of consciousness.
- Rhabdomyolysis: This is a medical condition associated with high tissue temperatures, for example during Heat Stroke, and prolonged physical exertion, which can result in the breakdown of muscle and subsequent organ damage.
If a worker develops signs or symptoms of Heat Stroke or Heat Exhaustion, the employer should provide immediate emergency medical treatment by calling 911 and taking steps to cool down the worker. Non-life-threatening heat-related illnesses may be treated with appropriate first aid measures.3
Tips for Employers to Follow the ANSI/ASSP Heat Stress Management in Construction and Demolition Operations Standard
A10.50-2024 includes several recommendations for programs that employers can put in place to help manage seasonal heat stress for construction and demolition operations workers, including a Heat Stress Management Program, which should be developed in consultation with a Qualified Person. ASSP states that “A Qualified Person is one who, by possession of a recognized degree, certificate, or professional standing, or who by extensive knowledge, training, and experience, has successfully demonstrated the ability to solve or resolve problems relating to the subject matter, the work, or the project.”3
The standard recommends that employers include the following in their programs:
- Methods to acclimatize new and returning workers to heat stress environments; for new workers, a period of five to seven days is recommended and for workers returning from a week or more away from work, a period of at least four days is recommended
- Methods to assess workers’ exposure to heat stress
- Requirements to provide portable water and, in certain instances electrolytes, to employees
- Development of an emergency action plan for heat-related emergencies, with on-site first aid; emergency services should be contacted for workers whose health is adversely impacted by high heat exposures
- Scheduled rest breaks and breaks for workers who are exhibiting heat stress symptoms
- Designated shaded areas for workers to rest
- Identification of on-site engineered and administrative controls – including proper personal protective equipment (PPE) to help reduce the risk of heat stress
- Methods to monitor workers’ heat strain, preferably through a buddy system approach
- Identification of employee participation and responsibilities
- Heat stress training on policies and procedures related to heat illness prevention and encouraging workers to identify signs and symptoms of heat illness; the standard includes detailed recommendations for Supervisor Training, Competent Person Training, Qualified Person Training, Employee Training, and Retraining Requirements
- Annual program review and revisions as necessary
The standard recommends that employers conduct a Heat Risk Assessment as part of the pre-task safety and health planning process. A Competent Person should perform a heat stress task hazard analysis prior to beginning work on any task with the potential for heat stress. According to ASSP, a Competent Person is “One who is capable of identifying existing and predictable hazards in the surroundings or working conditions which are unsanitary, hazardous, or dangerous to employees, and who has authorization to take prompt corrective measures to eliminate them.”3
This assessment may be conducted daily and considers factors such as ambient air temperature, direct sunlight, other sources of heat such as hot asphalt, air movement, humidity, physical demands of the work being done, working with limited rest breaks, extra clothing and PPE that impacts worker temperature and comfort, and limited access to drinking water and electrolytes.
PPE Solutions to Help Mitigate Worker Heat Stress
ANSI/ASSP A10.50-2024: Standard for Heat Stress Management in Construction and Demolition Operations notes that that process of controlling exposures to heat should follow the hierarchy of controls starting with engineering controls, followed by administrative controls, and then PPE.
PPE that is specifically designed to help reduce worker heat stress can help support employer-led Heat Stress Management Programs, as described in this standard. The MSA V-Gard C1® Hard Hat features ReflectIR® Thermal Barrier technology, which helps keep the inside of the hard hat up to 20°F cooler in sunny conditions.* V-Gard C1 hard hats also feature optional large vents with strategic placement for enhanced air flow, and a full brim with 12% greater coverage compared to a standard V-Gard® hard hat, allowing for additional shade and sun protection.
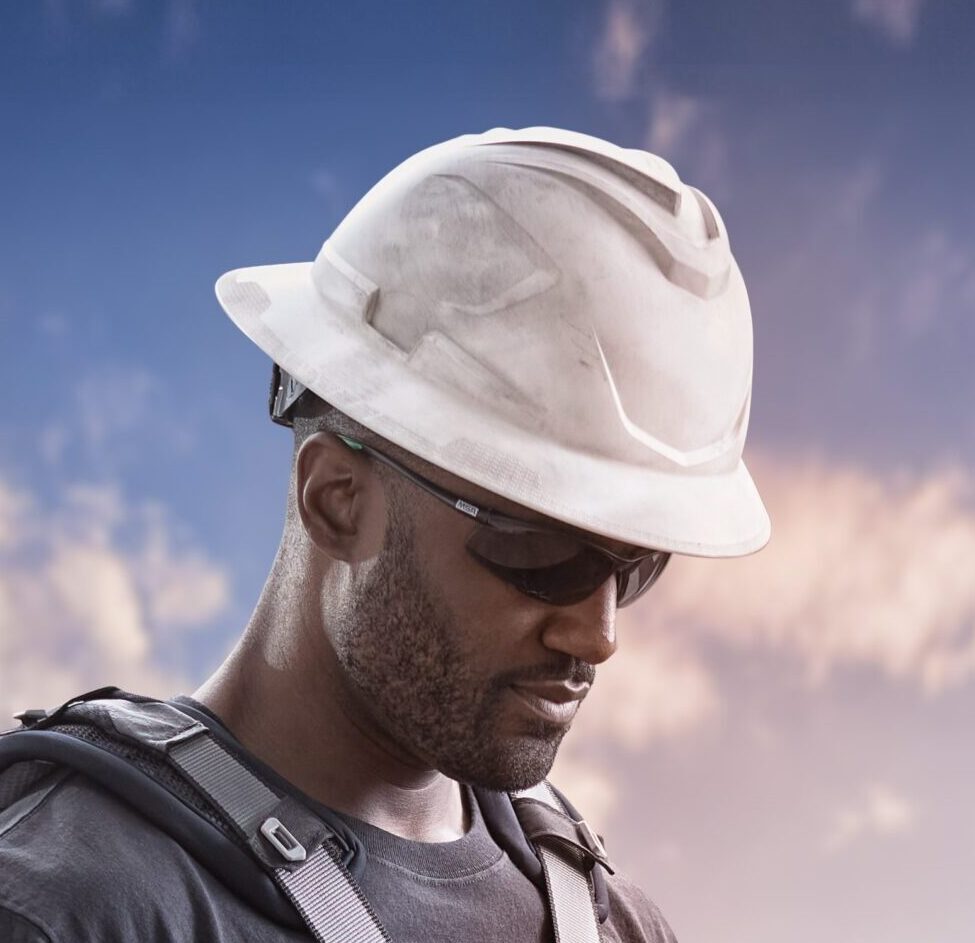
Explore more features of the V-Gard C1 hard hat.
EXPLORE MORESources:
1. https://www.osha.gov/heat/sbrefa
2. https://www.assp.org/news-and-articles/assp-publishes-first-standard-on-heat-stress-in-construction
3. ANSI/ASSP A10.50-2024: Standard for Heat Stress Management in Construction and Demolition Operations
*Compared to a hard hat without the ReflectIR Thermal Barrier in sunny conditions; testing done with black, non-vented, V-Gard C1 Hard Hats