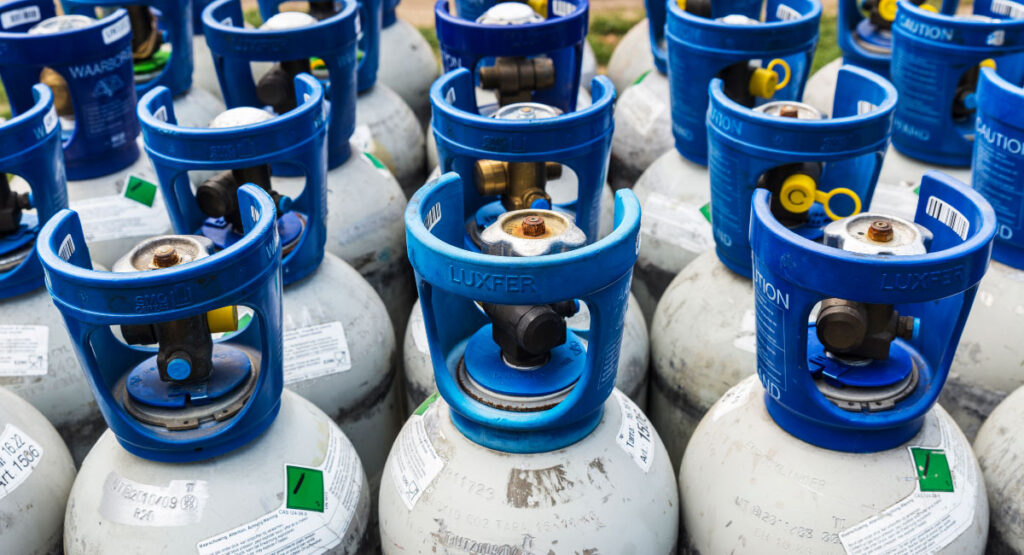
The global refrigerant market is evolving to incorporate a wider mix of refrigerant types, driven by the HFC phase-down outlined in F-Gas Regulations. As HVAC-R equipment design is modified for compatibility with mildly flammable refrigerants, gas detection may be required in multiple locations for different purposes. The transition to low-GWP alternatives, like A2L classified and natural refrigerants, introduces nuanced applications for sensors intended to help protect people, places, and the planet.
International Legislation Drives Refrigerant Evolution
For as long as the developing world has been using refrigerants and refrigeration technology, the chemical and behavioral characteristics of modern refrigerants have continued to change and evolve over time. In an advancing global society, refrigerants are critical materials for the purpose of human comfort cooling and refrigeration of goods in residential, industrial, and commercial settings. The industrialized era of the 1940s and ‘50s brought about the world’s first synthetic refrigerants. This enabled scaling to large HVAC-R systems as manufacturing, cold storage, and high-occupancy buildings created the need for efficient equipment. The emerging synthetic refrigerants, largely made up of chlorofluorocarbons or CFCs, were ultimately discovered to contribute to ozone depletion in the 1970s. As CFCs and HCFCs were adopted into modern systems, the environmental effects of refrigerant releases and emissions on the integrity of the ozone layer slowly became observable. Refrigerant blends were then reformulated to create another sub-category, HFCs, which do not deplete the ozone.
Even without having properties such as ozone-depleting substances, HFC refrigerants can still have an impact on the environment as greenhouse gases due to their high heat capacity. Major continental powers, such as the European Union and the United States of America, have created national legislation that supplements the Montreal Protocol treaty and establishes enforcement structures for the phasedown of HFC refrigerants. Europe acted to uphold the treaty by passing the F-gas regulation, which took effect on January 1st, 2015. The regulation was formulated with the goal of reducing emissions from fluorinated refrigerants to two-thirds of 2014 recorded levels by the year 2030. The regulation seeks to achieve this end by three methods: limiting the total amount of HFCs that can be sold in the EU, banning the use of F-gases in new equipment when alternatives are available, and preventing emissions of F-gases by requiring checks, service, and recovery of gases (European Commission).
In the United States, the schedule for phasing down production and utilization of HFCs follows the international timeline of the Montreal Protocol more closely. The passing of the American Innovation and Manufacturing (AIM) Act has empowered the phasedown on a federal level. It authorizes the US Environmental Protection Agency (EPA) to phasedown through production controls, refrigerant recovery, and equipment service requirements. It will continue approving alternative refrigerants via its Significant New Alternatives Policy (SNAP) program.
The EU provides a summary of climate-friendly alternatives to HFCs specific to certain applications and industries. In comparison, the US proposed rule for SNAP 26 identifies ten refrigerants which would be “listed as acceptable, subject to use conditions, in the Refrigeration & Air Conditioning sector,” (EPA). The proposal names specific refrigerant blends and includes guidance on the use of mildly flammable refrigerants. Through the initiatives driven by the EPA, the target goal of the AIM Act is to reduce the nation’s use of HFCs by 85% through 2035 and avoid an estimated 900 million metric tons of CO2-equivalent emissions.
As the industry strives towards the adoption of newer, mildly flammable refrigerants, the design of equipment and the safety standards governing acceptable use conditions will likely be updated and eventually harmonized.
The A2L Classification and Regulatory Environment
As new refrigerants are brought to market, they are listed and classified in ASHRAE Standard 34 (2019). The ASHRAE 34 Standard Committee determines toxicity and flammability classification. ASHRAE organizes each refrigerant on the market into a safety classification category based on its behavioral characteristics that impact the equipment design in which it is used, as well as its potential impact on personnel who are exposed to it. The safety classification chart designation for many of the low-GWP HFO blends is “A2L” (see Figure 1), which means it has moderate properties of flammability and low toxicity. Toxicity is classified based on Occupational Exposure Limit (OEL). Flammability is classified based on a flame propagation test, lower flammability limit (LFL), heat of combustion (HOC), and maximum laminar burning velocity (BV) (ASHRAE).
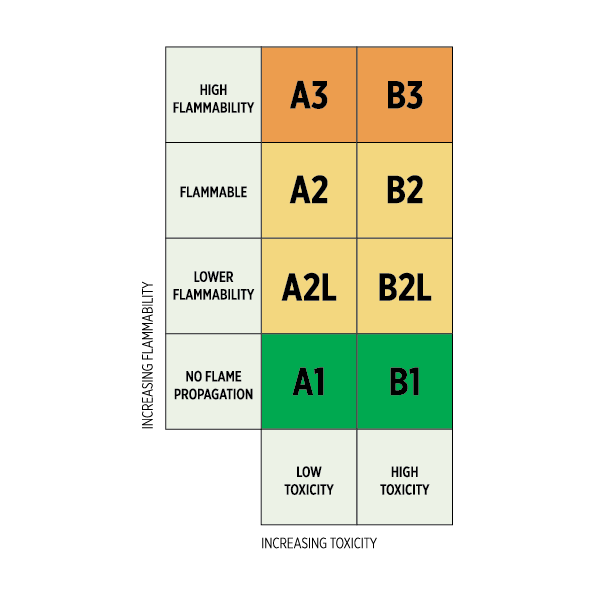
Considering that HVAC-R equipment design will often require adaptation for the variation in properties of the refrigerant, many safety standards are being drafted, modified, or expanded to guide design principles. Many of the standards combine scientific research with technical and industry expertise in an effort to capture comprehensive guidelines for the safe design of equipment that uses new refrigerants with increased flammability properties. These standards, which often have published versions that continue to evolve through amendments and revisions, are developed by international and regional bodies such as the IEC (International Electrotechnical Commission) and the US Underwriters Laboratories (UL).
Although A2Ls have been integrated into HVAC-R equipment and the international market for many years, regional regulatory environments will be developing and maturing to allow for the further adoption of A2L refrigerants. Once the standards have consensus, their specific requirements are often incorporated into the building and fire codes that are enforced by the relevant authorities. In the US, A2Ls are well underway to incorporate in the codes, with the ICB, IFC, and IMC planning to incorporate approvals for usage of A2Ls in the 2024 edition. For the UK and EU, the Institute of Refrigeration (IOR) has produced guidance to the EU Pressure Equipment (Safety) Regulations and Pressure Equipment Directive (PED).
Now that equipment manufacturers and the regulatory environment at large are gaining more insight into working with A2L refrigerants, the manufacturers of peripheral components, including gas and leak detectors, are also closely following the development of safety standards and requirements. Regulatory efforts to approve new A2L refrigerants are currently underway and expected to be finalized over the next few years. As A2L refrigerants become more commonplace, specific leak detection strategies may be necessary to help ensure operational safety.
Integrated Gas Detection Differs from Personnel Safety Detection
The adoption of A2L refrigerants sets a focus on establishing guidelines intended to mitigate flammability risks. However, there often still remains a need to help protect occupants from gross leakage levels that approach toxicity limits in an occupied space. The OEL exposure and toxicity levels outlined by OSHA are different by orders of magnitude from scientifically derived flammability limits for A2L refrigerants. The 8-hour time-weighted average (TWA) exposure limit often ranges between 500 – 1200 parts-per-million (ppm), but the LFL for most A2Ls ranges close to 100,000 ppm. For this reason, gas detection can be applied at multiple levels separately yet simultaneously; sensors may warrant being both integrated within the equipment and installed at fixed points in the greater occupied space.
In order to detect potential leakage in the equipment and mitigate flammability concerns, international and regional regulatory agencies often require integrated gas sensors that create an alarm condition in the case of an increase in the concentration of refrigerant before it accumulates to reach the Lower Flammability Limit. The primary safety standards set forth in these requirements are IEC / UL 60335-2-89 and 2-40, which call for multiple points of detection along the refrigerant circuit, from the compressor to the condensing unit to the case itself. The sensors must create an alarm condition, along with the initiation of controlled mitigation protocols, if refrigerant concentration approaches 25% of the LFL at any point in the circuit. This detection architecture ensures that flammability limits are not approached within the equipment and that any resulting hazards are successfully prevented.
Smaller leaks and slower accumulation of refrigerant in the greater occupied space, however, will not usually trigger the equipment-integrated sensors to alarm. This is often the case with walk-in coolers and freezers, where cold storage settings and mechanical rooms with HVAC equipment might be needed to maintain refrigerant concentrations below the 8-hour TWA OEL levels. Safety standards such as ASHRAE 15 and EN 378 govern specific gas detection requirements to help achieve this end. With first-level alarm settings often configured and set below 1000 ppm, diffusion-based point detectors are installed at fixed locations in the potential leak path to enable compliance with regulations and activate mitigation actions when the concentration nears or exceeds the Occupational Exposure Limit. In this way, a dual approach to gas detection can achieve the maximum level of protection for the occupants from both the toxic and flammable properties of any A2L refrigerant.
In conclusion, the strategic and dual-pronged approach to gas detection can help enable safe operational conditions for HVAC-R equipment designed to use mildly flammable refrigerants. While the OEL and LFL applications differ from each other, both can be incorporated into equipment design and building management controls to help safeguard people, places, and the planet through the evolution of refrigerants now and in the future.
Sources
- AHRI, “Chemical, Physical, and Environmental Properties of ASHRAE 34 and ISO 817” (https://www.ahrinet.org/system/files/2023-06/Ch2-Chemical_Physical_and_Environmental_Properties_of_A2L_Refrigerants_0.pdf)
- Federation of Environmental Trade Associations Ltd (FETA), 2017 “An introduction to A2L refrigerants and their use in Refrigeration, Air Conditioning and Heat Pump applications” (https://www.refcom.org.uk/media/1202/an-introduction-to-a2l-refrigerants-final.pdf)
- Tomohiko Imamura, Kyoko Kamiya, Osami Sugawa, Journal of Loss Prevention in the Process Industries, Volume 36, July 2015, Pages 553-561 “Ignition hazard evaluation on A2L refrigerants in situations of service and maintenance” (https://www.sciencedirect.com/science/article/abs/pii/S0950423014002344)
- “Transitioning to Low-GWP Alternatives in Commercial Refrigeration.” U.S. Environmental Protection Agency, October 2010 (https://www.epa.gov/ozone-layer-protection/transitioning-low-gwp-alternatives-commercial-refrigeration)
- Rajendran, Rajan. E360 Outlook, May 2022. Emerson.“Evaluating the current and future role of A2Ls in commercial refrigeration” (https://e360hub.emerson.com/qualifying-a2ls-refrigeration-solutions/laying-the-foundation-for-a2l-adoption)
- Hoying, Denise. E360 Outlook, February 2022. Emerson. “A2L Refrigerant Leak Detection” (https://e360blog.emerson.com/leak-detection-takes-precedence-in-emerging-a2l-systems/)
- Cika, Jim and Tara Lukasik. Building Safety Journal, January 6, 2022. “Code changes on A2L refrigerants” (https://www.iccsafe.org/building-safety-journal/bsj-technical/code-changes-on-a2l-refrigerants/)