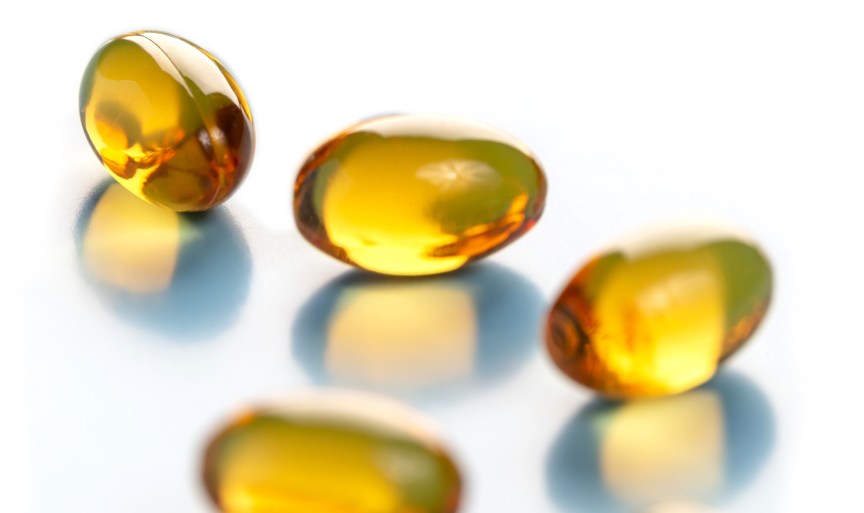
Improved Quality of Nutraceutical Edible Oils with Neutronics
A large manufacturer of nutraceutical edible oils located in the North East region of the US was having difficulties providing a consistent and reliable way of maintaining the high quality of their oils during packaging into gel capsules. Neutronics was able to review the processes involved and provide a cost effective solution.
A nutraceutical is a fortified food or dietary supplement that provides health benefits in addition to the basic nutritional value. Recent research cites that the global nutraceuticals market size is expected to reach US$ 403 Billion by 2024 from US$ 266 Billion in 2018. However, with such a rapid increase in market size, it is important to ensure product quality at all times. This is especially true for companies that greatly value consumer satisfaction and also want to maintain a competitive edge.
With consistent quality being an issue, a nutraceutical edible oils manufacturer turned to Neutronics for support. Neutronics Inc. is a world class provider of gas analysis and gas handling equipment technologies that include inerting systems for a variety of industries including food and nutraceuticals. The Neutronics’ Gas Analysis Solutions division designs, manufactures and commissions oxygen analyzers & ambient gas monitors to control oxygen and other gases during the manufacturing processes and was able to closely review the manufacturer’s processes.
Through careful analysis, it was found that the oil was becoming rancid through unwanted oxidation and therefore unacceptable for sale to their customers due to poor quality. The problem was being caused by exposure to air and moisture during the packaging process of their oils into gel capsules. With a clear diagnosis, Neutronics was able to develop a custom made solution.
Challenging Requirements
The customer had a number of unique requirements that made fitting an Inerting Control system (ICS) to their batch processing much more challenging.
The oils were manufactured in small batches, in portable tanks that had removable lid covers. Due to the tanks being portable, the sensors had to be easily removable so they could be moved from tank to tank as they were used, emptied and replaced with full ones. Having removable lids added the potential for gas leaks in or out of the tanks that had to be taken into account during system design. Another complication was that given the small size of the tanks and the variety of products being manufactured, several tanks had to be monitored simultaneously. All this also had to be done at a reasonable cost and within a budget.
Prototyping and Development
A Neutronics field engineer initiated the work by developing and installing a prototype in one of the tanks to test the conditions of operation. This allowed the engineer to determine the best location for the oxygen sensor, the flow rate of the nitrogen and where it was fed into the tank. It also evaluated the leak tightness of the tank itself.
After a number of trials, the prototype work showed the feasibility of the ICS, the estimated flow of nitrogen needed and helped in making design suggestions to modify the lids with seals that would improve tightness.
Service and Solution
Using the information generated on-site by the prototype, Neutronics designed a multichannel system that was capable of receiving input from several tank sensors simultaneously, and could independently and automatically control nitrogen flow into each tank as needed. The sensor leads into the tanks were attached using off-the-shelf sanitary fittings that allowed for them to be easily moved from tank to tank while keeping cost low.
Project Background
Many materials and products, as those in the food, pharmaceutical and nutraceutical industries, can be adversely affected by exposure to ambient oxygen and moisture. This exposure can cause a reduction in stability and potentially alter color, flavor, and aroma.
There are several ways to eliminate this problem, with the use of dry nitrogen to blanket (or “pad”) the process equipment, storage vessels and containers being one of the most effective methods. Other gases such as carbon dioxide or argon could also be used, however, nitrogen offers the advantages of being widely available, having low reactivity and being relatively low cost.
Inerting provides control of the concentration of oxygen in the vapor space around the product by dilution with nitrogen (or other inerting gas). It can also create a slight positive pressure in the tank preventing air and its accompanying moisture, and thus their potential degradation effects, from entering the process.
Inerting can be accomplished by simply having a sufficiently large volume of nitrogen flow over the top of the tank; however, this can lead to high nitrogen usage and therefore, higher costs. There would also be no certainty that products were actually being properly blanketed since the actual oxygen concentration would not be known due to factors like fill level, weather and other conditions. A more efficient way of accomplishing inerting would be to measure oxygen levels at the head space of the tank and control nitrogen flow to keep oxygen below the specified required maximum. This way, no nitrogen would be wasted regardless of the fill level of the tank while maintaining contaminants out.
Most standard ICS installations are composed of the same basic components as seen in the diagram (BELOW). They can be configured in different ways depending on the customer’s specific needs. Note that if there is a chance of exposure to any flammable or explosive gases as those seen in class 1, div. 1 type areas, intrinsically safe configurations for the units are also available.
Neutronics Inc. can engineer a complete system that will consist of one or more oxygen sensors, a suitable sample preparation package and the rightanalyzer with a control feedback loop that can regulate the flow of nitrogen into the tank. All of this tailored to the specific requirements of the process being monitored.
Oxygen Sensor: the element in direct contact with the sample that will emit a proportional electrical signal in response to the presence of a concentration of oxygen in the gas sample.
Analyzer: the electronic hardware that will take the signal from the sensor and convert it into one of several types of outputs, as for example a green/red warning light or an audible alarm, a numeric screen display of the amount of oxygen in PPM or percentage, or a 4 to 20 mA signal that can be sent to other devices for recording or to trigger operator alarms or other notifications. The analyzer can also interpret the sensor data and determine whether nitrogen flow is needed or not, and even actuate a flow valve to make the process completely automatic. Analyzers can come in a variety of models depending on the accuracy required and the number of inputs and outputs needed, from a single channel in and out to several depending on the number of tanks or devices being protected.
Sample Conditioning Unit: is the hardware that will remove the sample from the tank’s head space, either using a positive displacement pump, venturi effect or other means. It will also clean, filter, cool and dry the gas sample and deliver it to the oxygen sensors. Optional available filters allow for the unit to work even in very adverse environments.
The Result- Improved Quality of Nutraceutical Edible Oils
Gus Rolotti, Neutronics Field Sales Engineer comments, “The complete ICS has been installed and operational at the oil processing facility for over a year already.” He continues, “The customer reports that product quality has been kept at predictable levels thanks to their ability to control oxygen and moisture in the tank regardless of the ambient conditions.”
The customer also reported that the sampling equipment has been simple to use and has not experienced any technical issues or problems. The only work required by the customer has been standard maintenance to replace the oxygen sensors at the end of their expected life. The system has already paid for itself by eliminating out-of-spec product. An additional benefit is related to the nitrogen supply itself. By being able to control the flow of nitrogen as needed by the process, its total usage is lower and more predictable resulting in overall nitrogen savings.
Improved Quality of Nutraceutical Edible Oils Through Continuous Direct Oxygen Measurement and Controlled Tank Blanketing
Download a copy of the Neutronics, Nutraceutical case study now