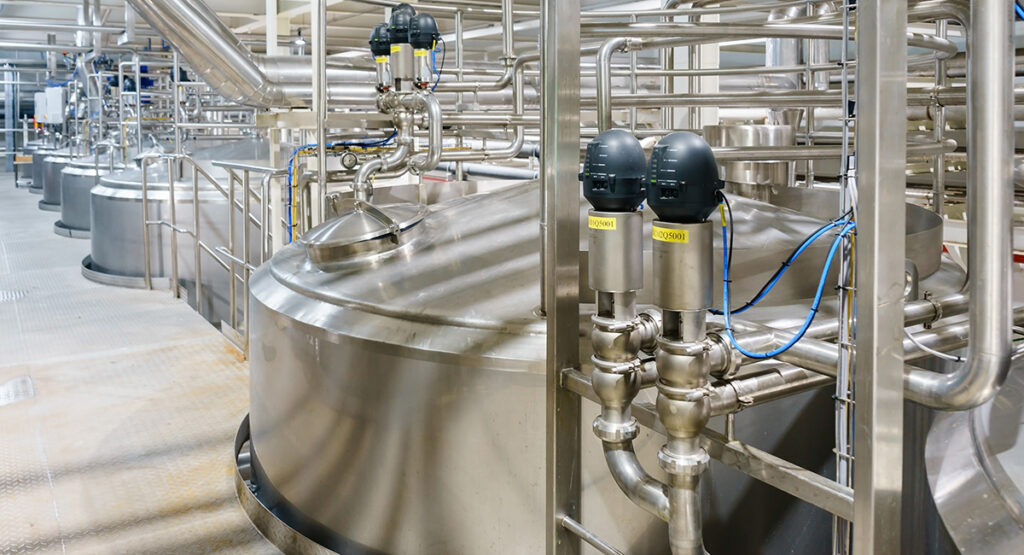
Choosing the right oxygen sensor for your gas analysis application is imperative. With multiple configurations to choose from, paired with the right technology, and ensuring proper use with gases or liquids; it can be a confusing process. Bacharach’s Gas Analysis Experts compiled this article to help you make the right decision based on your needs.
Sensing technology, by far, is a leading factor when choosing the right oxygen sensor. They can be separated based on their principle of operation, such as Optical, Paramagnetic, Eletro-Chemical, and Zirconium Oxide. The following summary outlines the differences in technology for the different sensors:
Optical: | LED light hits a membrane coated with luminescent dye. The dye will shine dimmer as the concentration of oxygen increases. An optical filter can measure the amount of light emitted and provide a value corresponding to the oxygen level. |
Paramagnetic: | Two glass spheres filled with nitrogen are aligned in a strong magnetic field. When they are exposed to a gas containing oxygen, the spheres are pushed out of alignment by an amount proportional to the amount of oxygen in the sample. |
Electro-Chemical: | An anode/cathode pair is submerged in an electrolyte solution. When oxygen in a sample galvanically reacts with the anode, it produces an electrical current proportional to the level of oxygen in the sample. |
Zirconium Oxide: | A Zirconium Oxide probe, coated on opposite ends with platinum, is heated to about 650°C. At this temperature, the probe becomes porous, allowing oxygen to travel from a high to a low concentration, producing a voltage proportional to the difference in concentration. When placing the probe between air and a sample gas, for example, the difference in concentration can be calculated based on the voltage generated. |
When selecting a sensor, although the type of technology it uses is important, there are a number of other considerations that must be taken into account. Several questions must be answered, and based on the answers, the user will have to decide what sensor provides the best compromise for the situation. A particular sensor will typically excel at one area, while rendered limited in a different area. Here are the right questions to ask:
What accuracy is needed?
Does the application require a sensor that can go down to low ppm, or even ppb, or will a percent type reading be sufficient? A need for low ppm readings would exclude a paramagnetic sensor; however, if the reading needs to reach ppb levels, then only a Zirconium Oxide type may do.
Is initial cost a concern?
There is a bit of a compromise between initial cost and overall ownership cost. The Electro-Chemical and Zirconium Oxide sensors are much cheaper than an Optical or Paramagnetic sensor; however, they will have to be replaced with new ones within 6 to 9 months in the case of Electro-Chemical sensors, or 3 to 10 years for Zirconium Oxide sensors. Optical or Paramagnetic sensors are not consumed and therefore could last for a very long time, but their initial cost is very high.
What other gases or contaminants may be present along with Oxygen?
Some gases are simply not compatible with some sensors. For example, Zirconium Oxide sensors are not recommended when hydrocarbon vapors or highly flammable materials may be present since they need to be heated up to 650° C and could ignite the material being sampled. Paramagnetic sensors are adversely affected by paramagnetic gases.
In addition, all sensors are affected to some degree by some contaminants that could be present in the sample gas. For cheaper sensors like the Electro-Chemical type, it may be just a matter of replacing the sensor with a new one, but in the case of Optical or Paramagnetic sensors, expensive maintenance may be needed to clean and remove anything that is fouling the surfaces.
How easy is it to perform maintenance on the systems?
Replacing an Electro-Chemical sensor may be just a matter of twisting the sensor free from the base, and snapping a new one in. However, the sensor may be located in an area difficult to reach, or maintenance personnel may not be available. In a case like that, it may be easier to have a system that does not need to be handled for a longer time.[
In short, there isn’t one “best” sensor for all applications. Each case needs to be evaluated carefully and all the questions answered to determine the best solutions for the application.
For support with your gas analysis application, reach out to one of our Gas Analysis Experts now.