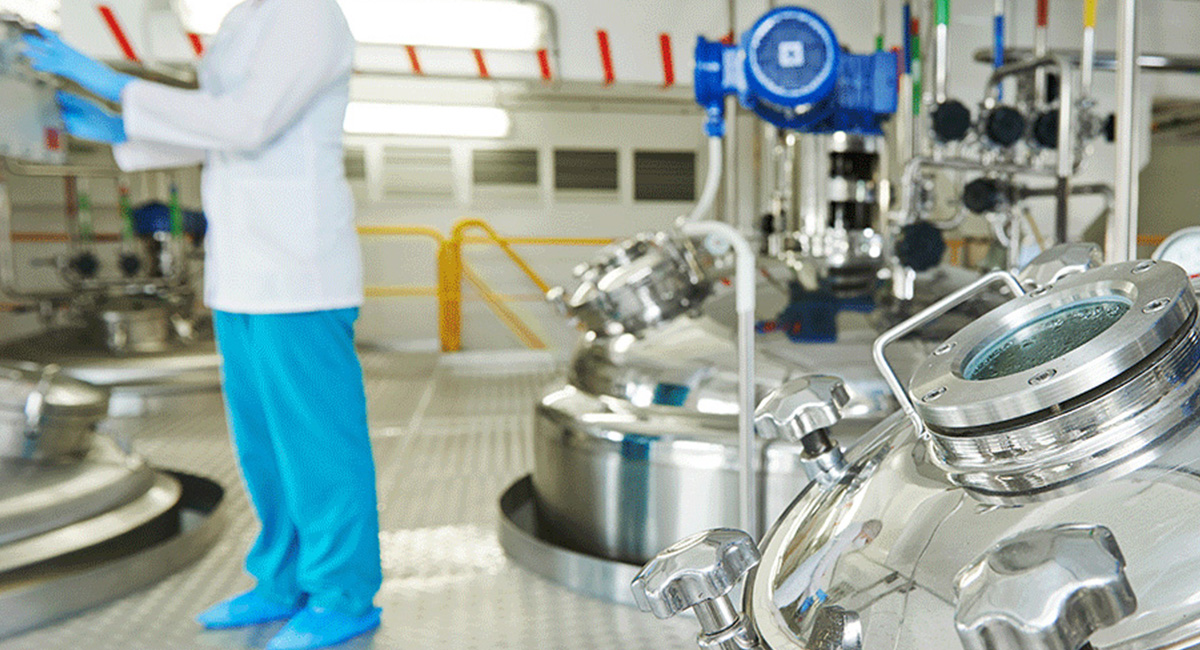
One purpose of tank inerting / tank blanketing is to reduce, or eliminate, the chances of a fire or explosion in the headspace of virtually any type of vessel such as tanks, containers, mixers, reactors, blenders, or similar. If oxygen were to reach the level at which the mixture becomes flammable, it is just a matter of a spark, heat build-up, static electricity, or similar to create an unsafe and dangerous situation. The best way to eliminate this risk is to displace enough oxygen with inert gas, like nitrogen, in the headspace. There are other reasons for inerting a tank, such as preserving product quality by avoiding oxidation of edible oils. However, the general principles of operation, as explained below, are the same.
The goal is clear: to replace some or most of the oxygen with an inert gas such as nitrogen. The two most popular and reliable methods this is accomplished are via a pressure-based blanketing valve or using an analyzer/sensor based system.
Blanketing Valve
The blanketing valve is directly connected to the vessel’s headspace where it senses its pressure. If it detects a decrease in pressure, it will open a path to allow nitrogen to flood the space until the set pressure is reached again. In this way, regardless of the level of the contents of the tank, or in case of a leak, opening of a hatch for refilling, or other, the appropriate pressure of the blanketing gas is maintained.
Analyzer / Sensor
The analyzer option works in a similar way, but instead of measuring the pressure, the sensor measures the level of oxygen in the space. If the amount of oxygen is above the set level, it will send a signal to open a solenoid valve that would allow nitrogen to flood the vessel until the oxygen reaches the set limit again.
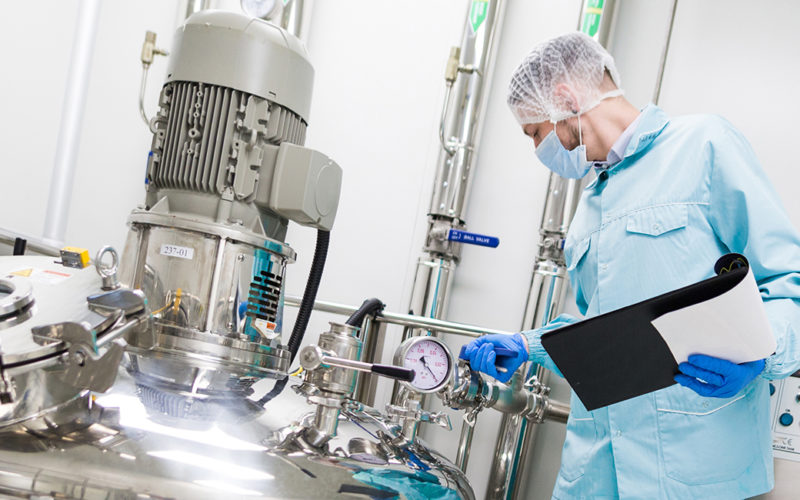
When the blanketing valve is used, it is necessary that the system be first brought down to an inert point, otherwise, it will simply maintain the pressure of the headspace regardless of the content of oxygen. The system on its own is incapable of determining if it has truly achieved an inert atmosphere or not. To reach an inert atmosphere, it is necessary to flush the vapor space with sufficient nitrogen. There are a number of publications that will provide detailed information on how to calculate the number of volume changes required before that happens. If a vessel has not been conditioned, it will not be truly protected.
The analyzer/sensor combo also needs to start with an inert atmosphere, however, it will know when it has been reached since it automatically senses the oxygen and will continue to supply nitrogen until the desired level of inerting is reached. The system itself will know when it has reached the setpoint. This ability to respond to a pre-established setpoint is valuable in cases when a level of oxygen other than zero needs to be maintained. This occurs in certain chemical reactions where it is necessary to have a low level of oxygen, but still have some present to allow for the reaction to take place. Blanketing valve systems are more or less all or nothing type of inerting systems.
It is because of this feature, that the analyzer/sensor system can achieve savings in the amount of nitrogen used while at the same time providing an exact indication of the level of oxygen present.
On the other hand, the blanketing valve provides for a simpler set up, uses no consumable components, like the sensors, and its initial cost is lower than that of an analyzer. For non-critical vessels, where the initial cost is an issue and the amount of nitrogen used is not a concern, this may be the best option. However, for critical systems, where oxygen needs to be closely controlled, the best option is the analyzer/sensor combination.
Both system types offer valuable and important safety/quality enhancement to the vessel they are added to. Although both achieve the same general goal, each offers different advantages. Careful consideration is encouraged when selecting one method for a particular application.
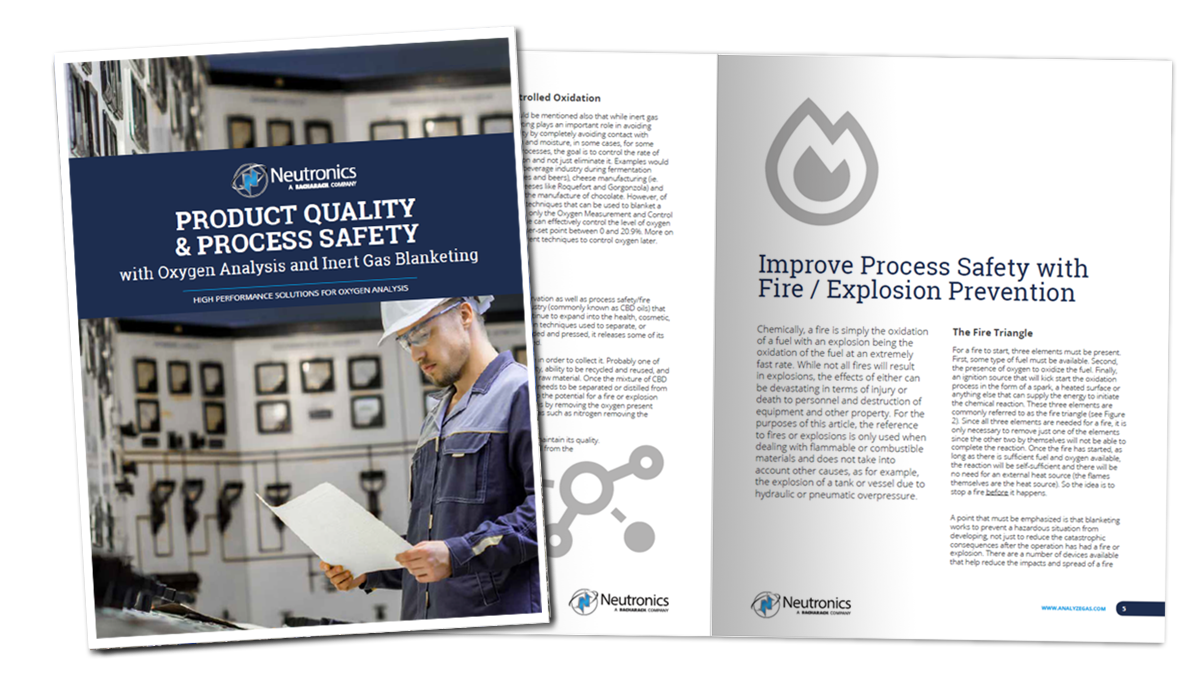
Read More about inerting control with the Product Quality and Process Safety Whitepaper.

Looking to specify or plan tank blanketing for your processes? Read our Tank Blanketing Whitepaper.